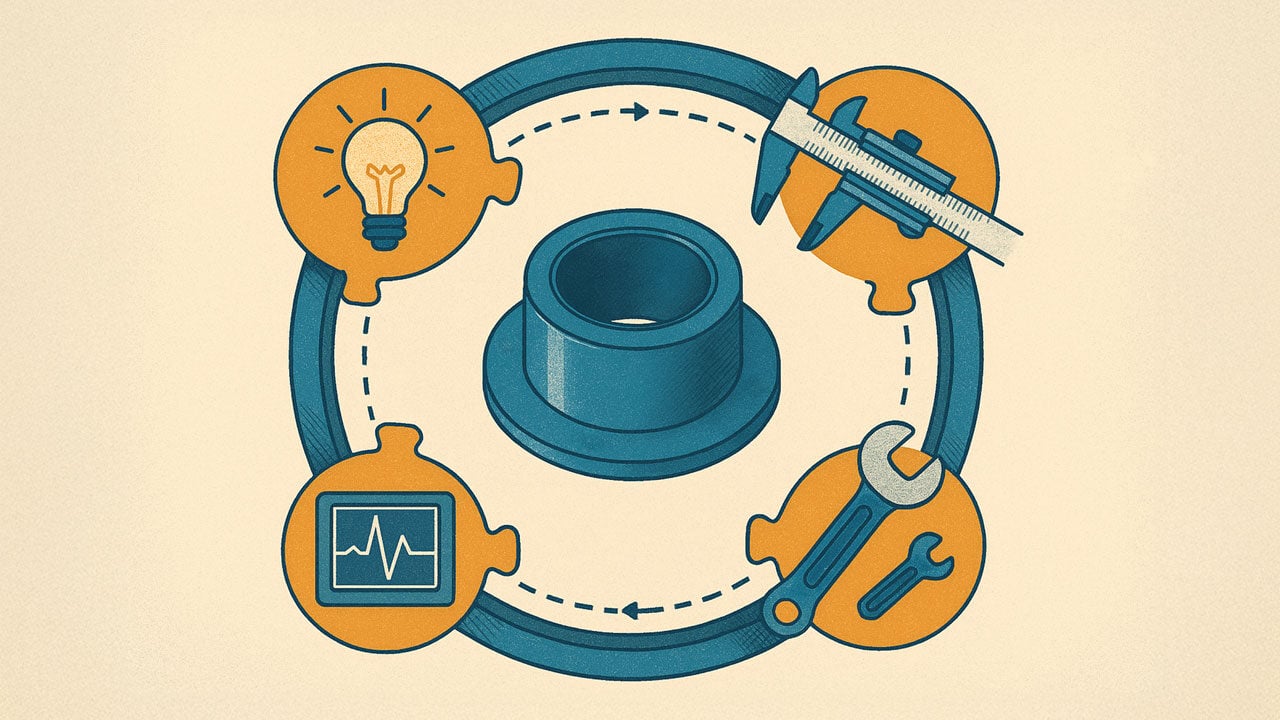
2 min read
An All-Phase Commitment to Value-Added Engineering
At TriStar, engineering support is not something customers need to request separately. From early application reviews to long-term troubleshooting, our team is structured to provide engineering insight at each step. This commitment applies whether...
Read More