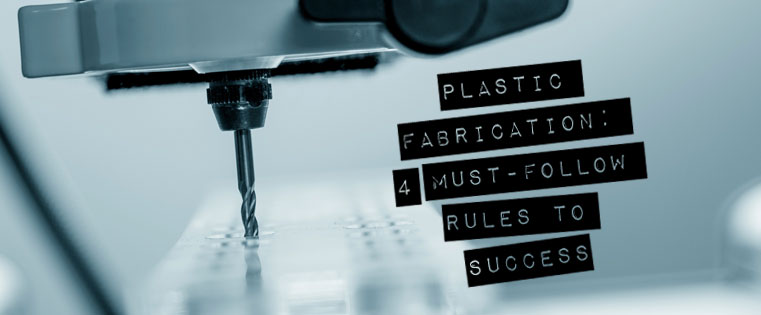
Have you ever fabricated plastic components?
For many traditional machine shops, metal is an easy and familiar material to work with, but plastic fabrication presents a whole new set of challenges. Metal is a solid material and predictable to machine, while plastics are a hybrid of different materials, and change shape as they are machined. Simply stated, the basic principles of machining metals do not apply when machining plastics. And any mistake in plastic fabrication can also result in expensive scrap loss.
How can you master the art of plastic fabrication? We have 4 must-follow rules to success.
Metals are generally easy to machine; they don’t creep or change shape as you fabricate. Plastic materials are prone to substantial creep and can easily melt and chip during machining. Yet with the right tools and techniques, plastic fabrication can be achieved by following these four golden rules:
1) Choose materials wisely
Plastics are high-performance and an excellent replacement for bronze, stainless steel and cast iron. They excel in high-temperature and extreme working environments. But choosing the right material is critical, since some high-performance formulas are substantially more expensive than metal. For instance, Polybenzimidazole (PBI-Celazole) is 25x the price of cold-rolled steel, and 15x more costly than Type 303 stainless steel.
When choosing plastics, remember that the materials you choose are an investment in performance. Choosing a higher-quality (more expensive) material will yield a higher-quality part. And higher-quality parts can save you from field failures or costly recalls down the line. Find the right bearing material from the materials database.
2) Limit heat
Heat buildup is the number one cause of failure in plastic fabrication. In fact, the very act of machining generates friction ― or heat. Without the right machine speeds/feeds and coolants, plastic cutting tools can actually become plastic melting tools. Heat also presents dimensional challenges, which makes it more difficult to hold tolerances. Special attention must be paid to limit heat.
3) Determine the best fabrication technique
Which machining technique is best for you material? Sawing? Milling? Drilling? Threading or tapping? Often, the right technique comes down to the category of plastic you are working with; either thermoset plastic or thermo plastics. Thermoset plastics retain their solid state indefinitely, while thermoplastics can be melted more than once to form new shapes. Thermoplastics are best suited to machining.
4) Beware of burrs
Burrs are a common machining hazard and can ruin surface finishes. They usually occur when a machining tool reaches a travel end without additional support. Techniques to avoid burring can take more time, but the time saved in deburring may pay for the longer machining cycle. Avoiding burrs can help you reduce the costs and obtain an optimal finish.
Is in-house plastic fabrication the right choice for your material application? Or would you be better outsourcing this service? Get our copy of our Plastics Machining Guide to help you decide. Or just connect with the Plastic Fabrication Experts to answer your questions!