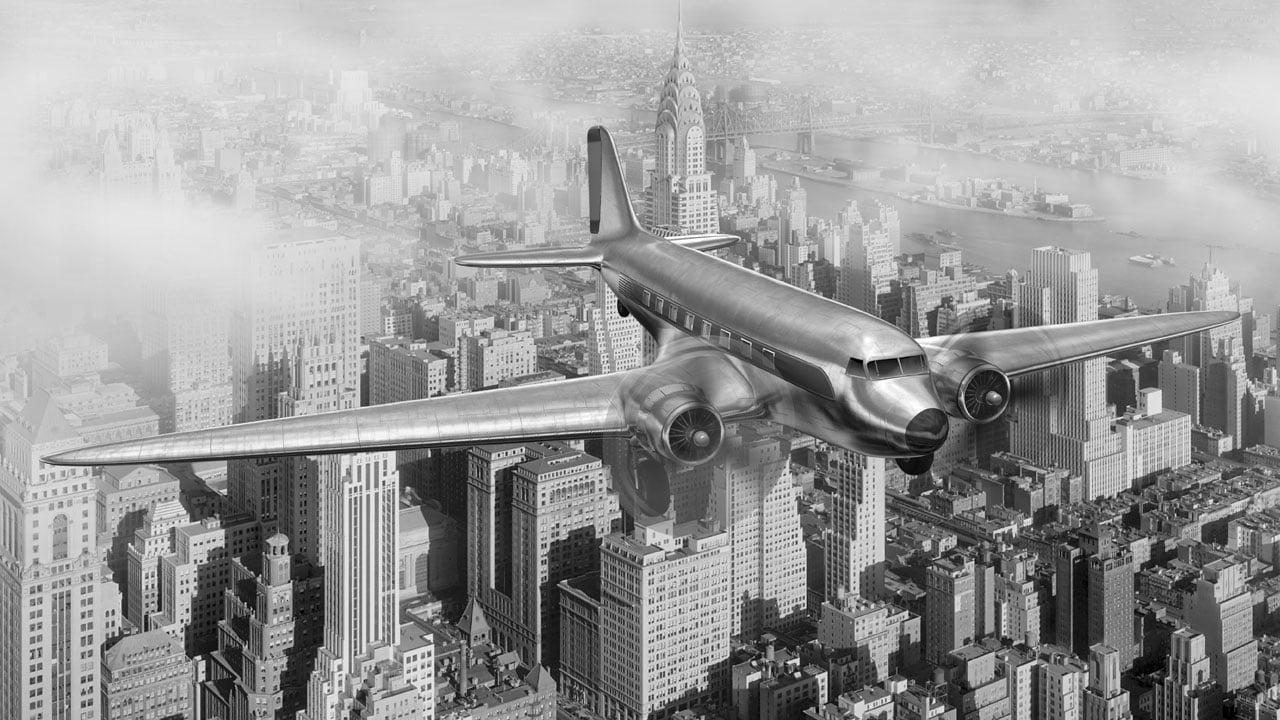
3 min read
Materials Engineering in Aerospace History
Since the first plane was constructed by the Wright Brothers with the tools, wood, and canvas available at an early 20th-century bicycle shop (plus a built-from-scratch 12-horsepower engine), aerospace advancements have always been constrained by...
Read More