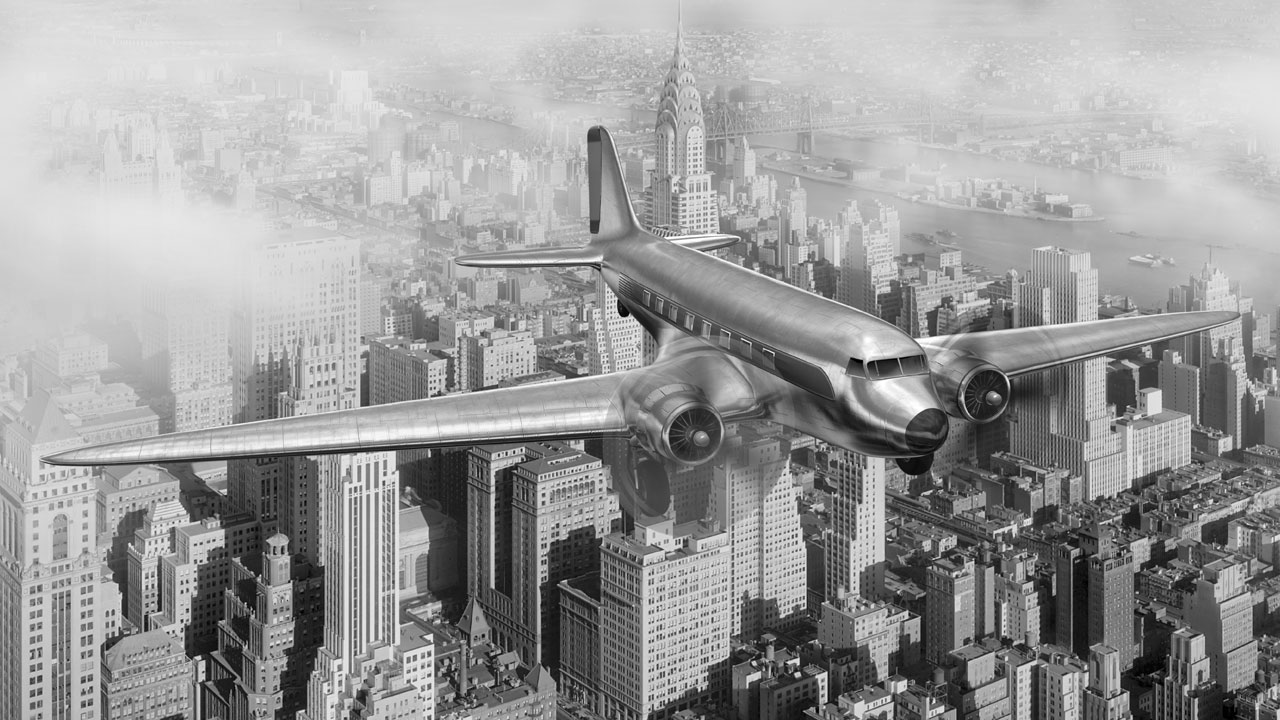
Since the first plane was constructed by the Wright Brothers with the tools, wood, and canvas available at an early 20th-century bicycle shop (plus a built-from-scratch 12-horsepower engine), aerospace advancements have always been constrained by the available materials. New materials would be critical to letting aircraft fly faster, higher, and further than ever in the coming decades. At the same time, the aerospace industry has also taken a lead role in pioneering a number of advanced materials that have proved valuable across a variety of other industries.
In this blog, we explore the historical relationship between advancements in materials engineering and innovation in the aerospace industry. Of course, the milestones below provide only a quick survey of a century’s worth of scientific advancement, but they serve as a powerful illustration of why the right materials are so critical in aerospace.
Milestone One: From Wood to Steel
The Wright Brothers’ pioneering aircraft was no exception; all early aircraft were made from the lightest materials available at the time, wood (the Wright Flyer used spruce) and canvas, with steel wires used for primitive control surfaces. Even as the applications for aircraft exploded during World War 1, wooden construction remained the only option for aircraft manufacturers.
To some early aircraft designers, adopting metal for flying machines seemed like madness: why adopt a heavier, more expensive material? German aviation pioneer Hugo Junkers would be the first to engineer a practical all-metal aircraft in 1915. His legendary J1 (nicknamed the “sheet metal donkey”) was a revolutionary design that was also the first aircraft to be made using a monoplane wing design (all previous aircraft had employed a biplane design, which helped provide structural rigidity for wooden aircraft but increased drag). The steel J1, however, was heavy and had poor handling characteristics. Junkers would need a lighter material to usher in the metal age in aerospace.
Milestone Two: Aluminum Lets Aerospace Metal Go Mainstream
At about a third the weight of steel, aluminum offered the perfect material to kickstart a new era in aerospace engineering. This material would dramatically expand the possibilities for air transportation, and Junkers released the world’s first true airliners, like the F13, by 1919. The Ford Trimotor (often considered the first mass-produced airliner) followed close on Junkers’ heels, and the 1930s would see an explosion in more practical, cost-effective commercial aircraft designs. By 1935, the legendary Douglas DC-3 entered service (it remains so to this day) and the modern airline era was in full swing.
Milestone Three: Composite Materials
According to an Airbus history, fiberglass was the first lightweight composite material to be used in aircraft, first employed in the 1940s for fairings, noses, cockpits, and later for the rotor blades of early helicopters in the 1960s. Since this early application, carbon fiber composites have become increasingly critical to aerospace designs. Offering a weight advantage over aluminum, composite materials are taking over as a higher and higher portion of total airframe structures. In 2009, the 787-8 Dreamliner became the first aircraft to have wings and fuselage made from carbon-fiber polymers. Advanced military designs like the Tiger helicopter, are made from over 80% carbon fiber, while even civilian aircraft like the Airbus A350X WB are over 50% composite material. Ceramic metal composites, meanwhile, are critical for withstanding the extreme temperatures found within jet engines.
TriStar is proud to support the aerospace industry with composite solutions like Ultracomp and CJ Composite.
Milestone Four: The Space Race Fuels New Material Innovations
The space race fueled an incredible quantity of R&D spending, and materials engineering was no exception. One important example is polyimide materials, which have a long history that dates back to the 1960s, when they were originally developed by NASA and the Langley Army Research Center (LARC) as a space program heat shielding material. Today, TriStar leverages the Meldin® 7000 series polyimides, developed by St. Gobain, in a variety of aerospace applications (you can even find Meldin in space!). Learn more about this versatile family of materials in our overview here.
How Performance Polymers Contribute to Continued Aerospace Advancements
Of course, the advancements discussed above represent only a few of the many materials advancements driven by the aerospace industry. Today, a huge number of materials are used in aircraft construction including nickel, graphite, steel, numerous aluminum alloys, and a growing number of ceramic composites and carbon-fiber polymer composites. Titanium is employed for a large number of components on military aircraft but remains a relatively high-cost option. And 3D-printed materials are quickly finding a home in aerospace.
If you are interested in a deeper look at the biggest challenges for aerospace industry materials (and how TriStar’s high-performance polymers can help solve them) please see our guide here, based on knowledge gleaned from successful engagements with a variety of aerospace industry clients.