Aerospace Industry Components: Key Challenges and Solutions for Polymers
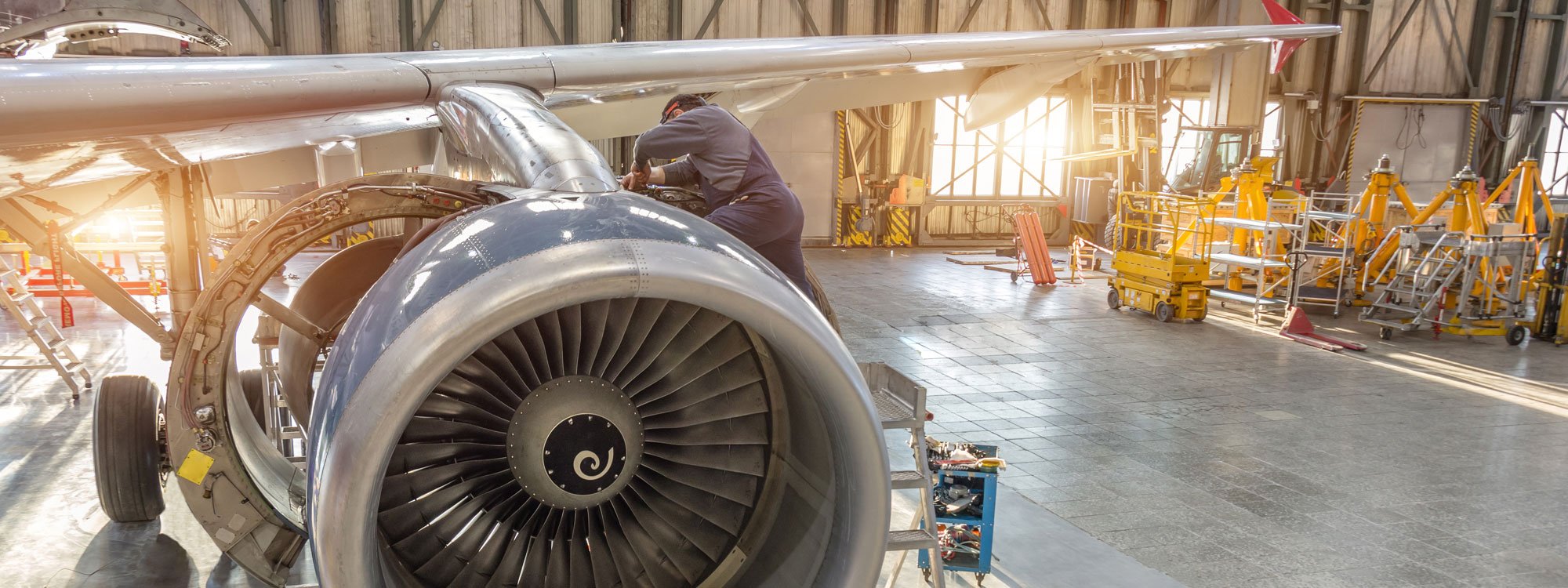
Until two bicycle makers, Orville and Wilbur Wright, took to the skies of North Carolina just 120 years ago, many thought human flight was fundamentally impossible. An incredible wave of global innovations followed in the Wright Brothers’ wake, and the aerospace industry quickly became one of the defining pillars of the modern era. In the matter of just a few years, powered flight went from science fiction to a vital cog in global defense and transportation systems:
- Within just 8 years of the Wright Brothers’ first flight in 1903, aircraft were first used in active combat in the Italian-Turkish War. Military applications would dramatically expand in the First World War just a few years later, with the first air-to-air kill recorded in 1915. Only 13 years passed between Kitty Hawk and dogfights over Europe.
- In 1914, the first fixed-wing scheduled airline began operating. By 1919, planes were capable of crossing the Atlantic. In the wake of World War 2, a surplus of aircraft, pilots, and new designs kicked off an unprecedented boom in aviation, and the 1950s would see the birth of the jet age for commercial airlines.
- In 1947, Chuck Yeager broke the sound barrier in manned flight for the first time, and Yuri Gagarin would become the first human to orbit the earth in 1961. In 1969, Apollo 11 reached the moon less than 70 years after the first powered flight.
Prefer to read this later? We'll email you a PDF.
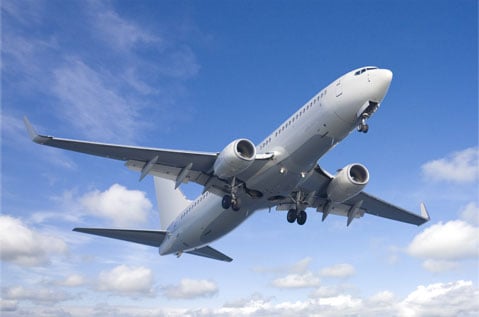
During this astonishing century of incredibly rapid innovations, the aerospace industry both spearheaded and benefited from parallel advancements in materials science. The Wright Brothers’ aircraft was made from wood, canvas, and other materials available around a bicycle shop.
In the decades since, aerospace advancements have drawn on just about every category of material in existence, from aluminum alloys, to composites, to advanced polymers. The right materials are vital for standing up to unique operating conditions while delivering the outstanding reliability that is so critical for aerospace components. We take a deeper look at the historical relationship between materials and aviation advancements in our blog here.
In this guide, we provide a high-level overview of the aerospace industry today, with a focus on the biggest challenges faced by aerospace equipment and components. From there, we take a more granular look at how TriStar’s portfolio of high-performance polymers can be leveraged to solve tough aerospace engineering challenges.
Aerospace Industry Overview
Even today, the aerospace industry is always evolving, as the recent growth of unmanned vehicles (UAVs) and private space exploration demonstrates (we take a look at the most important trends in today’s aerospace industry in our blog here).
Today’s aerospace industry is incredibly diverse, including everything from giant global aircraft and engine manufacturers to small aftermarket part suppliers for general aviation. According to data from the International Trade Administration, the United States’ aerospace sector directly employs over 500,000 workers and produces the highest trade balance (over $75 billion in 2019) of any US manufacturing industry. Learn more in our aerospace industry overview blog here.
The broader aerospace sector may be divided into sub-industries as follows:
- Commercial Airlines, including large commercial aircraft manufacturers like Boeing and Airbus, and the many OEMs who support them.
- General Aviation manufacturers and OEMs, who supply the vast array of fixed- and roto-wing aircraft used in recreation, utility applications, emergency services, and transportation.
- Airport Infrastructure, including the vast array of ground logistics and infrastructure required to keep fleets of aircraft safely in the air.
- Unmanned Aerial Systems (UAS) manufacturers, which comprise a rapidly growing market segment providing everything from advanced industrial and military drones to small photography and recreational units.
- Military Aircraft, the largest single segment of the US aerospace industry.
- Rockets and Space: while traditionally dominated by defense contractors, this market segment has recently seen increasing market share won by private contractors such as SpaceX, Boeing, and Virgin Galactic.
In this guide, we focus on commercial aerospace applications. Looking for information on defense applications? Please see our guide here.
Across all of these market segments, even the smallest aircraft has an incredible number of subsystems and underlying components. From landing gear, to avionics, to jet engines, every aspect of an aircraft must be engineered to exacting standards.
Space: TriStar Polymers’ Final Frontier
We take pride in being able to say that TriStar materials are found everywhere from under the ocean to outside Earth’s atmosphere. Space applications create unique challenges for materials, in addition to those associated with the broader aviation industry. For example, materials like Meldin are capable of resisting outgassing in a vacuum—critical for spacecraft components.
TriStar products are found on the satellites of a leading European aerospace manufacturer, where Fluoroloy® H provides superior thermal conductivity for high-power microwave amplifiers, just one of many TriStar products in space. Learn more.
Important Engineering Challenges for Aerospace Industry Components
Aerospace components (and the materials used to manufacture them) must stand up to an incredible variety of conditions while maintaining reliability—the safety of crews and passengers depends on it. Aircraft cannot be maintained while in use, and part reliability has a direct impact on maintenance schedules, downtime, and ultimately the economic viability of operating any commercial aircraft.
- Aircraft components must exhibit exceptional reliability over a long working lifespan—10,000 flight hours is a common target for commercial aerospace components.
- In many applications, the materials used in aerospace components need to offer exceptional and highly predictable wear and friction resistance.
- Aircraft maintenance is expensive and keeps aircraft from staying in the air and generating revenue. For this reason, aircraft components need to provide the lowest possible maintenance expenses.
- Aerospace engineering is extraordinarily precise, and an aircraft’s constituent components need to meet tight tolerance standards to ensure reliability, predictable performance, and most of all safety.
- Components employed in many parts of an airframe must be able to resist failure or deformation under a broad temperature range. The atmosphere can be frigid at altitude, while components experiencing high-speed friction may be exposed to extreme heat: the standard range of temperature tolerance for aerospace components is -70°F to 190°F. For components used in and around the engine compartment, this range is even greater, from -70°F to 550°F.
Across all of these requirements, aerospace materials engineering is always about tradeoffs. Aerospace engineers face the challenge of maximizing reliability, achieving the desired performance characteristics, and minimizing costs—all while keeping weight as low as possible.
High-Performance Polymers in the Aerospace Industry
TriStar’s engineering team has experience working with a number of different aerospace companies to source the right materials for a variety of different components. Our deep arsenal of high-performance materials and custom engineering capabilities help clients find solutions to all of the common aerospace engineering challenges outlined above. A few of our top materials for aerospace applications include:
Rulon
A family of proprietary PTFE materials, Rulon is engineered for an exceptional combination of high compressive strength, a very low coefficient of friction, and excellent abrasion and corrosion resistance. These attributes make Rulon a great choice for a variety of aerospace applications.
You can learn more about Rulon here.Meldin
The Meldin® family of materials includes polyimides that provide high-temperature performance ideal for aerospace components requiring exposure to extreme temperature ranges, such as engine components. Meldin can withstand continuous operating temperatures from cryogenic ranges through 600°F, and intermittent exposure up to 900°F.
Learn more about Meldin in our complete guide here.Ultracomp
This versatile composite is available in a number of different grades, allowing its mix of strength, stability, and corrosion resistance to be specified to meet the requirements of a variety of aerospace applications.
Learn more about Ultracomp in our product page here.CJ Composite
CJ composite provides an excellent choice for aerospace applications that put a premium on low friction, high load capacity, strong wear resistance, and low maintenance.
Learn more about CJ Composite here.
Other TriStar materials used in aerospace applications include TriSteel (used in landing gear guide sleeves) and components for dielectric applications, made from combined ceramic-PTFE materials like Fluoroloy.
For a deeper look at specific material specifications, please see our interactive materials database here.
When demanding aerospace applications require performance beyond the capabilities of our off-the-shelf materials, TriStar’s enhanced materials division is here to help. For example, plasma treatment can promote better bonding on metals in a variety of different components. Surface treatments may also be used to, for example, improve the bond-ability of elastomers for over-molding. Learn more about plasma cleaning in our case study here.
Case Studies: Aerospace Materials Engineering Success Stories
Rulon Goes Supersonic
Challenge: One TriStar client is working to push engineering boundaries as they develop a novel approach to supersonic aircraft. Their goal? Aircraft designs that go faster and travel further than conventional commercial airliners today. To succeed, they needed to find the best approach for reducing friction between composite parts that would rub together across hundreds of takeoff and landing cycles.
Solution: Our engineers recommended Rulon J friction rub strips for aircraft panels and components exposed to friction. Its special fillers reduce the friction of mating hardware, including the composite-on-composite or composite-on-metal friction commonplace in lightweight aircraft designs. By lowering friction and heat levels, Rulon J adds stability to extend the overall service lifetime of each component.
Learn more in our case study here.
Finding the Right Material for High-Temperature Engine Components
Challenge: TriStar worked with a major commercial jet engine manufacturer to engineer a vane bushing component capable of withstanding high-temperature locations within a modern turbofan assembly. The right material would need to resist melting, offer high thermal oxidative stability, and be compatible with prolonged exposure to aerospace fuels and oils.
Solution: TriStar’s engineers studied the operating requirements of various engine designs and specified Meldin® 7021 as the appropriate solution. This grade of Meldin is ideally suited for high-temperature aerospace applications, and bushings made from Meldin® 7021 now provide a bearing surface for vanes inside these engines, promoting longer life and reduced maintenance requirements.
Learn more in our case study here.
Helping Vintage Planes Soar
Challenge: DHC-2 Beavers have been a mainstay of the vast, wild Alaskan wilderness since the 1940’s. A leading Alaskan air charter company worked with TriStar to find the best material to help extend the life of these valued vintage aircraft, which have been out of production for decades. Stainless steel flight control bearings were succumbing to erosion in the face of wet, icy, conditions, and a better material was needed.
Solution: TriStar corrected this design flaw by retrofitting stainless bearings with custom Ultracomp UC 300 composites. The composites have excelled through several years of flight tests in all weather conditions.
Learn more in our case study here.
Interested in learning more about how TriStar materials have been applied across a variety of aerospace applications? Explore our full aerospace case study library here.
Other Aerospace Application Examples
Because TriStar’s high-performance polymer components can be engineered to accommodate a wide range of challenging operating conditions found in aerospace applications and offer a lighter weight than metal components (even the heaviest TriStar material is only 3x the weight of water), they can be found in a wide variety of aerospace applications:
- Landing Gear, which make use of TriStar materials in seals and bearings for oleo struts, guide sleeves, hydraulic valve seals, and piston slide rings.
- Avionics, which employ TriStar components in wire/cable clamps, navigation electronics, connector insulators, communications subsystems, and security subsystems.
- Fastening Systems including dielectric insulators, rivet installation robotics, engine components, and high-temperature thread locks.
- Body components that put a premium on friction resistance, including rub strips, engine link wear components, thrust reverser wear liners, and high-temperature thread locks.
- Flight controls employ TriStar materials in seals and bearings for valves, actuator cylinders, and fuel delivery systems.
- Group support and assembly fixtures, where TriStar materials can be found in high-strength fixture bearings, axle jack systems, and auxiliary power units.
Learning More: Consultative Aerospace Materials Engineering
We hope this guide provided a helpful overview of the importance of advanced materials like TriStar polymers in aerospace applications, and how they can be used to tackle some of the toughest engineering challenges in the industry. The aerospace industry has an extraordinary diversity of applications and operating environments, and no single material is a cure-all. Ultimately, materials need to be carefully matched to the challenges of the operating environment where they are expected to thrive.
Rather than treating aerospace components as commodities to be sourced from the cheapest bidder, our experience suggests that an engineering-driven approach that carefully aligns components to the challenges at hand will almost always pay off over the long term. A nominally cheaper component will be far more costly over its lifetime if it fails prematurely or creates the need for extra maintenance work.
TriStar brings a true consultative engineering approach to our relationship with each and every client. We work hard to understand not just where materials can function, but where they can solve problems.
If you have questions about how the right materials can help solve engineering pain points for your aerospace equipment or components, we invite you to reach out to our team using the button below.
Frequently Asked Questions
Here are a few common questions relating to the content in this guide.
Q: What trends are reshaping aerospace components today?
A: Growth in unmanned aerial systems and the rise of private space contractors are expanding demand for advanced, lightweight components. Across segments, engineers are pursuing reliability, lower maintenance, and tight-tolerance performance in harsh environments—driving adoption of high‑performance polymers and composites in structures, controls, avionics, engines, and support systems.
Q: What core engineering challenges do aerospace parts face?
A: Components must deliver long service life, predictable low friction and wear, tight dimensional tolerances, and dependable performance across extreme temperatures. Commercial targets often span thousands of flight hours, while many parts see conditions from frigid altitude to engine‑adjacent heat—pushing materials toward engineered polymers and composites over traditional options.
Q: Why choose polymers and composites for aircraft systems?
A: High‑performance polymers/composites reduce weight, support tight tolerances, and provide excellent wear and friction behavior with strong corrosion resistance. Lighter components help minimize maintenance and downtime pressures while maintaining reliability—key advantages for landing gear, flight controls, avionics hardware, and engine‑adjacent parts where metals add unnecessary mass.
Q: Where are TriStar materials used on modern aircraft?
A: TriStar materials appear in landing gear seals and bearings, avionics clamps and insulators, fastening systems, engine components, body rub strips and wear liners, flight‑control valves and actuators, fuel delivery, and assembly fixtures. The breadth reflects configurable grades that meet specific load, wear, tolerance, and temperature demands across aircraft subsystems.
Q: How does Rulon improve aerospace sliding interfaces?
A: Rulon proprietary PTFE materials combine very low friction with high compressive strength and excellent abrasion and corrosion resistance. That balance suits rub strips, sliding panels, and composite‑on‑composite or composite‑on‑metal interfaces—stabilizing motion, reducing heat, and supporting long service life in aircraft structures and control surfaces.
Q: What makes Meldin a fit for high‑temperature aerospace?
A: Meldin polyimides provide high‑temperature performance from cryogenic ranges through approximately 600°F continuous, with intermittent exposure up to about 900°F. They also address space‑specific needs like resistance to vacuum outgassing—making Meldin a strong option for engine components and space‑exposed parts requiring dimensional stability and thermal endurance.
Q: When should we specify Ultracomp composites?
A: Ultracomp offers configurable grades to dial in strength, stability, and corrosion resistance for demanding aerospace environments. It’s well suited to applications where you need composite bearings or structural wear components tuned to exact operating conditions without sacrificing weight targets or dimensional control across varying temperatures and loads.
Q: What advantages does CJ composite bring to bearings?
A: CJ composite bearings emphasize low friction, high load capacity, strong wear resistance, and low maintenance. These traits make CJ a practical choice for critical sliding or oscillating interfaces where predictable tribological performance and reduced service requirements help keep aircraft available and maintenance costs controlled.
Q: How do polymers support aircraft weight objectives?
A: TriStar’s lightweight materials contribute to overall weight reduction compared with metals while still meeting load, wear, and tolerance needs. Even the company’s heaviest options remain significantly lighter than metallic counterparts—helping engineers hit performance targets without adding mass that can drive up fuel and maintenance costs.
Q: How does TriStar guide aerospace material selection?
A: TriStar applies a consultative engineering approach—aligning material and grade selection with each application’s operating environment, temperature window, load profile, motion type, and tolerance stack‑up. The focus is on solving reliability and maintenance challenges with the right polymer or composite rather than treating components as commodity parts.