Defense Components: Key Challenges and Solutions for Military Polymers
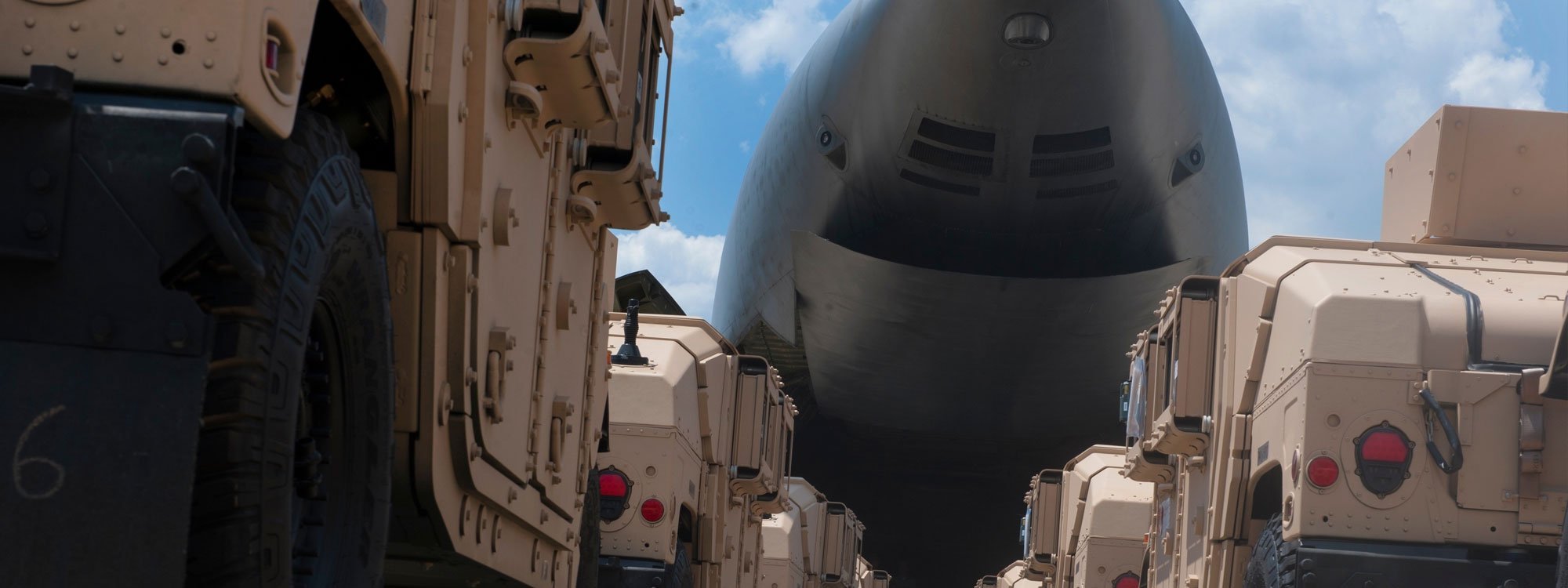
The men and women of the armed forces work hard to keep us safe and protect our freedoms, and they do so with the help of the most advanced array of technologies ever assembled. Standing behind the military’s incredible equipment and technologies are defense OEMs (Original Equipment Manufacturers) and civilian employees and researchers, who draw on advanced engineering and materials from across the globe to deliver rugged, reliable, and innovative military hardware.
Today, it is easy to take for granted that the U.S. defense industry is an economic linchpin and key technological innovator. But this status was only achieved as a result of a meteoric rise in the years since World War Two. “A hundred years ago,” Forbes notes, “the United States did not have a defense industry. At least, not in the sense that term is used today….”
But today’s defense industry has evolved into something far different: a permanent fixture of the civilian economy ($400 billion in annual contracts supporting about 200,000 defense OEMs) ready to support the U.S. armed forces across a variety of long-term global missions. For a broader overview of the defense industry’s historical evolution, please see our blog here.
Prefer to read this later? We'll email you a PDF.
In this guide, we provide a high-level overview of key challenges for defense components, followed by a deeper look at how TriStar’s portfolio of high-performance polymers have been leveraged to solve defense engineering challenges in applications ranging from remote sniper rifles, to robots, to World War Two vintage aircraft.
Defense Industry Overview
In many ways, military engineering challenges are more diverse than those of any other single industry or sector. Some military applications, like suspensions for land vehicles, have as much in common with the automotive industry as they do for the outgassing-resistant materials employed in satellites. Based on TriStar’s experience working with defense OEMs across a diverse set of projects, the following categories are helpful for making sense of the immense defense sector.
- Land and Maritime. This category refers to the broad array of non-armament defense equipment that must stand up to rugged wet/dry operating conditions but is not required to stand up to the unique operational requirements of aerospace equipment.
- Armament captures the array of systems used to target, launch, and deploy weaponry. Whether a ground-based system, ship-mounted, or aerial, these systems share common challenges related to sighting, target acquisition, and safe, reliable operation for the personnel deploying the relevant armament.
- Missiles and Aircraft Equipment. A variety of airborne defense components come with different requirements for weight, temperature resistance, and reliability compared to ground-bound systems. In this guide, we focus on defense-specific aerospace applications.
For a deeper look at the challenges specifically associated with aircraft components, please see our guide here. - Space. Defense equipment intended to operate in the vacuum of space
present unique challenges including extremes of cold/heat and exposure to
high-intensity gamma rays.
We provide a broader overview of the defense industry in our blog here. Across each of these broad categories, the safety of defense personnel depends on the engineering of components ranging from bearings to radomes.
Important Engineering Challenges for Defense Components
Across a huge range of applications, many of them highly specialized, lives may depend on defense industry components performing reliably when called upon. Military equipment must operate in a variety of conditions that would be considered prohibitive for civilian equipment, creating a need for uniquely rugged and high-performance materials. While every application is unique, the challenges below are common across most categories of defense equipment.
- Strong, predictable wear and friction resistance is critical for prolonging component lifespan and reducing premature failures in extremely rugged operating conditions.
- Extreme, varied, and unpredictable environmental conditions mean that many defense components must be engineered to thrive across wet/dry applications, dirty and abrasive environments, and temperatures ranging from frigid cold to the heat of a jet engine.
- Extreme tolerances must be maintained to maintain safety and efficacy for ultra-precise equipment like targeting systems, armaments, aircraft, and land vehicles.
- Chemical resistance. For example, missile and aerospace components must be resilient to certain fuels, cryogenics, and hydrocarbons.
- Ultra-reliability is critical for components where regular maintenance and replacement is not always an option. While the military often has an imperative to pursue even more aggressive maintenance schedules compared to civilian equipment, reliable components play a key role in minimizing downtime, reducing operating costs, and simplifying logistics.
The high-performance polymers highlighted below provide an example of why the right materials are essential for meeting this diverse set of engineering challenges.
High-Performance Polymers for Military Applications
At TriStar, our engineering team has engaged with a broad variety of defense applications to find the right materials for incredibly tough operating requirements. Our own arsenal of high-performance materials, coupled with our custom engineering capabilities, offer defense clients proven solutions to all of the common engineering challenges outlined above. Some of our most important materials for defense applications include:
Rulon
A family of proprietary PTFE materials, Rulon is engineered for an exceptional combination of high compressive strength, a very low coefficient of friction, and excellent abrasion and corrosion resistance. These attributes make Rulon a great choice for a variety of defense applications.
You can learn more about Rulon here.Meldin
The Meldin® family of materials includes polyimides that provide high-temperature performance ideal for defense components requiring exposure to extreme temperature ranges, such as engine components. Meldin can withstand continuous operating temperatures from cryogenic ranges through 600°F, and intermittent exposure up to 900°F.
Learn more about Meldin in our complete guide here.Ultracomp
This versatile composite is available in a number of different grades, allowing its mix of strength, stability, and corrosion resistance to be specified to meet the requirements of a variety of unique defense applications.
Learn more about Ultracomp in our product page here.Fluoroloy
Fluoroloy, available in various grades, is a family of materials custom-formulated for the sort of extreme and specialty sealing applications that abound in the defense industry. Including PTFE and PTFE blends, fluoropolymers, PEEK, and UHMW-PE, Fluoroloy offers broad chemical compatibility, can tolerate temperatures from -450°F to 600°F, and has excellent friction and wear characteristics.
Learn more about Fluoroloy in our comparison chart here.
Other materials that have proven their capabilities in defense applications include our CJ/FCJ composite line and Torlon
For a deeper look at specific material specifications, please see our interactive materials database here.
The defense industry often brings unique requirements to the table, and many of our defense projects draw on our custom engineering capabilities to find the right solution for incredibly unique challenges (we provide a number of interesting examples below). When our off-the-shelf materials cannot provide the right mix of characteristics, the enhanced materials division (EMD) is ready to step in.
Case Studies: Defense Components Engineering Success Stories
Eliminating Stick-Slip in Military Rifles
Challenge: an international manufacturer of remote sniper weapons (in this case, a .50 caliber semi-automatic rifle) was struggling with sticking in the mounting and pivot points of the rifle. They needed a trunnion bearing that was lightweight, durable, and would allow for smooth shooting and aiming of this remote weapon.
Solution: TriStar studied the application and identified our Rulon J material as a strong fit for all requirements. Rulon J is ideal for start/stop applications where any stick or slippage needs to be eliminated to ensure responsiveness and precision. As an added bonus, Rulon is self-lubricating, dramatically reducing maintenance needs for this weapon mount.
Learn more in our case study here.
Replacing a Legacy Material for the Iconic Boeing B-52
Challenge: The Boeing B-52 has been rumbling through the skies since 1952 and remains in active military service to this day (even though production ended in 1962). Keeping aircraft of this vintage in operation creates some unique engineering challenges. In this case, a critical material used in multiple locations on the aircraft was no longer being manufactured.
Solution: Boeing partnered with TriStar to find the right replacement material, and our engineering team hit the archives to study the original material’s formulation. After 2 years of testing and custom development work with our resin suppliers, TriStar was able to find a solution that could fulfill challenging requirements including a broad range of temperature resistance, amenability to machining into complex geometries, and excellent wear resistance across a 10-year service expectation.
Learn more in our case study here.
Supporting Rapid Deployment of Naval Craft
Challenge: The Mark V Special Operations Craft (SOC) offers a low radar signature for inserting SEALs and other special forces into incredibly dangerous mission areas, including the ability to launch SEAL Delivery Vehicles and UAVs. This craft employs advanced materials throughout its construction, and because it may need to be airlifted anywhere on earth at a moment’s notice, the design places a premium on sourcing the lightest weight components possible.
Solution: TriStar specified our Ultracomp composite bearings as an ideal fit for the high-load capacity, corrosion resistance, and lightweight required for the Mark V’s active suspension systems—used to rotate, slide, and position the boat inside a C5 transport plane. Ultracomp’s grease-free operation also reduced maintenance requirements for this system, while strong shock resistance helped reduce the risk of misalignment or separations.
Learn more in our case study here.
Interested in learning more about how TriStar materials have been applied across a variety of military applications? Explore our full defense case study library here.
Other TriStar Polymer Military Applications
Because TriStar’s high-performance polymer components can be engineered to accommodate the incredibly wide range of challenging operating conditions required by the military, they can be found in a wide variety of defense applications in addition to the case studies above.
Land and Maritime Components
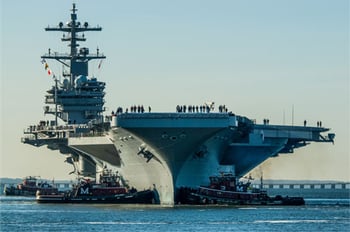
- Ground support systems, including weapon transport trailers, engine removal/install trailers, assembly fixtures, and more.
- Robotics, including everything from IED disposal bots to aerial drones.
- Shipboard systems, including missile launch devices, fire control systems, electronic countermeasure (ECM) devices, and ship-to-ship transfer equipment.
- Underwater technology, including winch systems, autonomous surveillance equipment, and recovery vehicles.
Armament Components
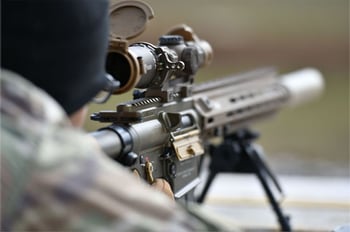
- Artillery and surface weapon systems, including components such as recoil suppression devices, T + E devices, and hydraulic lift/tilt systems.
- Sighting devices (FLIR), including both airborne and ground night vision, small weapons scopes, laser delivery systems, and security monitoring equipment.
- Hydraulic and pneumatic equipment, including control valves, solenoids, auxiliary pumps, and service equipment.
- Bomb racks and air launch systems, which depend on an array of components including compressor systems, linkage bearings, and linear slides.
- Electronic and radar components, which use components such as RF and microwave insulators, horns, standoffs, and radomes.
Missile & Aerospace Components
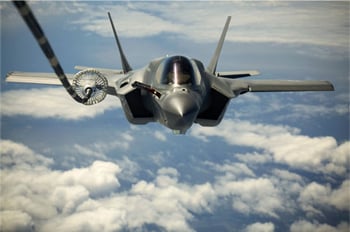
- Launch systems, including rocket fueling components, launch pad devices, compressor seals, and recovery systems.
- Missile control systems, which rely on tightly integrated guidance systems and flight-control systems (both mechanical and fluid-based).
- Electronics, including specialized solutions such as RF/microwave components and dielectric components for connectors.
Space Components
Space applications create unique challenges for materials, in addition to those associated with broader missile/aerospace systems. For example, materials used in aerospace (like Meldin) must be capable of resisting outgassing in a vacuum. Applications include:
- Satellite systems, including satellite repair solutions, gas analysis systems, RF components, and vacuum service components.
- Flight vehicles, including composite structural components and subsystems such as oxygen, onboard scientific projects, fluid recovery.
Learning More: Consultative Defense Component Engineering
TriStar is incredibly proud to support our military OEM customers who help keep our troops safe in dangerous missions around the world, and we hope this guide has provided a helpful overview of the importance of sourcing the right materials for military components.
To accommodate challenging operating conditions across a vast number of unique applications, military projects often call upon one-off solutions, custom engineering, and the most advanced materials. TriStar’s extensive array of materials and hands-on engineering approach has proven to be a strong fit for this environment. We recognize that no single material is a cure-all, and each component should be carefully aligned to the specific needs of the mission at hand.
TriStar brings a true consultative engineering approach to our relationship with each and every defense industry client. Our team is passionate about understanding not just where materials can function, but where they can solve problems.
If you have questions about how the right materials can help solve engineering pain points for your defense equipment or components, we invite you to reach out to our team using the button below.
Frequently Asked Questions
Here are a few common questions relating to the content in this guide.
Q: What engineering challenges do military defense components face?
A: Military defense components must operate reliably under a wide range of extreme conditions including rugged wet or dry environments, extreme temperatures, the need for chemical resistance, ultra-precise tolerances, and minimal maintenance opportunity.
Q: Which defense sectors impose unique material requirements?
A: Sectors include land and maritime systems exposed to harsh environments; missile and aircraft equipment demanding weight, temperature, and reliability standards; and space components requiring resistance to extreme cold or heat and gamma radiation.
Q: Why is ultra-reliability so important for military materials?
A: Ultra-reliability matters because many components must function in environments with limited maintenance access—so materials must remain dependable under stress, minimizing downtime and ensuring safety.
Q: What role does chemical resistance play in polymer materials for defense?
A: Defense components, especially missiles and aerospace systems, must resist fuels, cryogenics, and hydrocarbons—making chemical resistance a vital design requirement.
Q: What material properties help mitigate wear and friction in defense applications?
A: Components require strong, predictable wear and friction resistance to endure abrasive, rugged conditions and extend operational lifespan.
Q: How does the Rulon® polymer support defense component performance?
A: Rulon® offers high compressive strength, a very low coefficient of friction, and excellent abrasion and corrosion resistance—making it ideal for durable defense parts.
Q: In what temperature ranges does Meldin® perform effectively?
A: Meldin® polyimide materials can continuously operate from cryogenic temperatures up to 600 °F, and handle intermittent exposure up to 900 °F—suitable for high-heat defense environments.
Q: What is Ultracomp, and why is it used in defense applications?
A: Ultracomp is a composite bearing material designed for high durability in critical conditions. It delivers tailored performance benefits, making it a strong choice for demanding military applications.
Q: What are the benefits of Ultracomp for defense applications?
A: Ultracomp composite bearings offer engineered durability for mission-critical defense environments. Their composite structure supports consistent performance under rugged conditions, extending component life and reducing maintenance needs.
Q: How does TriStar position itself as a partner for defense materials?
A: TriStar collaborates directly with defense OEMs, applying advanced engineering and specialized high-performance polymers to meet rugged, mission-critical requirements.