4 min read
U.S. Defense Industry History: 240+ Years of Engineering Innovation
Dave Biering
January 10, 2024
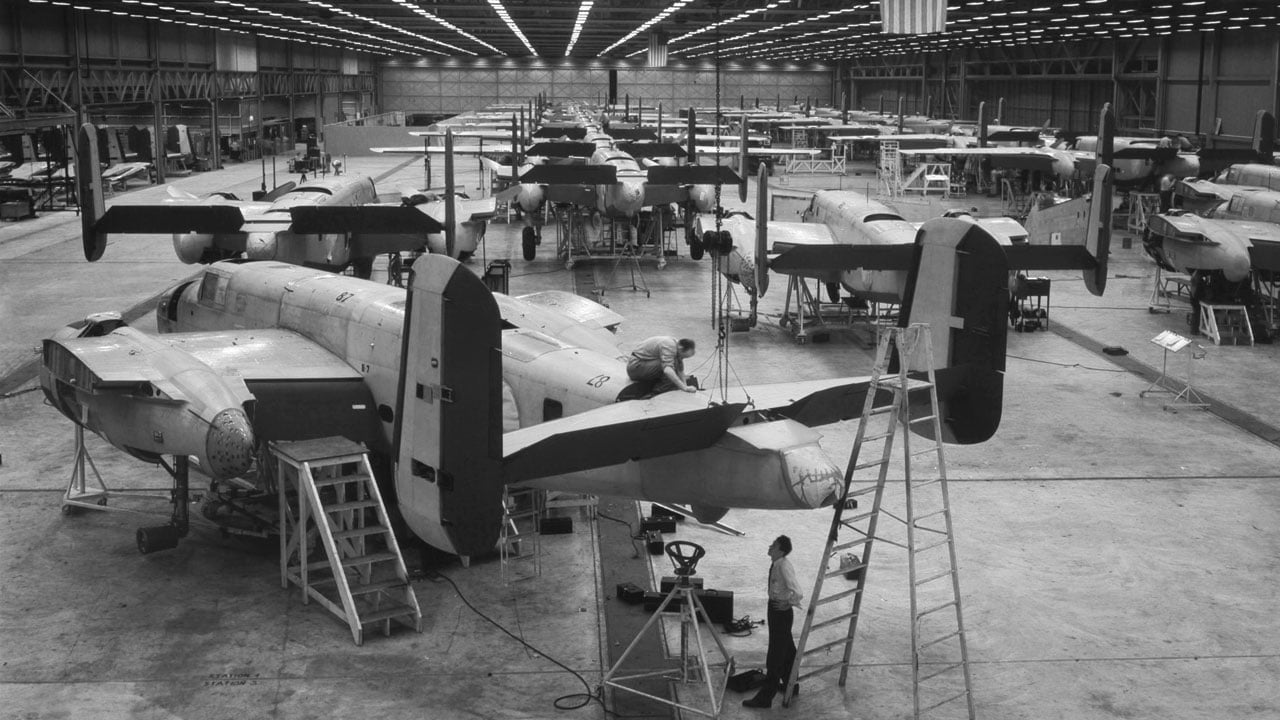
Since playing a part in the birth of interchangeable parts, the U.S. defense industry has always been at the forefront of global manufacturing and engineering innovation since its inception. But the defense sector has not always been the economic lynchpin it is today. In this article, we provide a concise overview of the U.S. defense industry’s historical development, with a focus on defense OEMs’ long history of spearheading manufacturing innovation.
The U.S. Defense Industry and the Birth of Mass Production
While the early defense industry was defined by just a few types of armament, namely rifles and artillery pieces, and largely confined to production in Army-owned arsenals, U.S. defense manufacturing still managed to be at the forefront of a manufacturing revolution.
The early history of the U.S. defense industry can be traced to George Washington’s creation of the Springfield Armory in Massachusetts in 1776. While initially only used for storage, the Library of Congress notes that the manufacture of muskets and other guns had begun by the 1790s. Legendary names like Henry Deringer and Eliphalet Remington had begun producing weapon components for the U.S. government by the early 1800s, and the Springfield facility was immediately innovating in pursuit of a more efficient division of labor:
“Once all parts of a gun were produced within a single establishment, the Springfield Armory and a small number of gun making outfits developed internal subdivisions and specialization in the manufacture of each part of the gun. For example, at the Armory, subdivision of labor increased rapidly; there were 36 occupational specialties in 1815, 86 by 1820, and 100 by 1825.”
By the 1830s, more legendary names had contributed to bringing true interchangeable parts to the U.S. armory system: Samuel Colt and Eli Whitney (also featured in our blog on agricultural equipment). Whitney’s early experiments with interchangeable parts in pistol production were a precursor to revolutionary firearms production at the Harper’s Ferry armory which relied extensively on interchangeable parts, originally pioneered by John H. Hall. More practical designs were perfected by Samuel Colt by 1850, and a new era in defense manufacturing had begun.
These early advancements in the U.S. arms industry were some of the first large-scale global success stories for interchangeable parts, as well as the accounting and factory management practices that would come to define the “American System” of manufacturing.
Toward a Permanent Military Industrial Base
Despite its manufacturing innovations, the early U.S. defense industry was not the economic powerhouse it is today. Rifles can be made to last for many years, and relatively modest peacetime production was sufficient to keep the military’s armories filled. During the Civil War, many soldiers on both sides depended on equipment from Europe such as England’s Enfield Rifle and the Austrian Lorenz rifle.
At this time, arms manufacturing would scale up for major conflicts but dramatically decrease in peacetime. Even in the wake of a major global conflict like World War One, observes Forbes, “the War Department had demobilized from nine million personnel at the beginning of 1919 to a mere 397,000 in 2023, and what remained of weapons production was largely confined to Navy shipyards and Army arsenals. That’s the way it had always been in America—minimal military outlays in peacetime, which ballooned when the nation went to war and then quickly reverted to one percent of the economy when peace returned.”
Notably, this level of expenditure simply was not sufficient to support a true peacetime defense industry. Weapons makers could not afford to maintain extensive production capacity at idle for years while waiting for the next war. Even after U.S. industry ramped up to supply the famous “arsenal of democracy” in World War 2, defense spending plummeted in the immediate aftermath of the war.
An in-depth history of Cold War era rearmament, published by the DoD, notes that when the Truman Administration kicked off its containment policy in the spring of 1947, the U.S. military was already a shell of its World War Two-era capabilities. In 1945, the US government spent $83 billion (of $93 billion total federal outlays) on defense and maintained 12 million uniformed Americans. By the time the Korean War began in June 1950, these figures had fallen to $12 billion and 1,459,000 uniformed personnel.
As US policymakers began to recognize the need for a sustained U.S. military buildup to not only meet the needs of the Korean War but keep up with the Soviet Union over the coming decades, the Cold War ushered in a new era for the U.S. defense industry. The new status quo was effectively codified by the Defense Production Act of 1950, which for the first time formally defined the defense industrial base, established a priority system for sourcing military equipment, and “provided for seed money to establish quantity production of new defense materiel and to increase production capacity for specific equipment through the improvement of production methodologies and facilities.” Moving forward, military expenditures would total over half of the federal budget (and typically around 10% of GDP) for the remainder of the Cold War period.
For the first time, civilian defense contractors could afford to sustain a large workforce in peacetime, R&D spending ramped up like never before, and defense OEMs would increasingly become key innovators for both defense applications and the civilian economy. Since the Cold War era, notes a report from the National Academy of Engineering, “technology development in the United States has historically been closely related to defense industrial policies,” although “during the Cold War, roughly two-thirds of U.S. R&D was funded by the federal government, primarily for defense. Today, that percentage has been reversed, with two-thirds of U.S. R&D funded by private industry.” Indeed a long list of innovations that define the modern era—including the internet, GPS, microwave ovens, super glue, and duct tape—have origins in defense-related R&D.
What trends will shape the defense industry for the next decade? Learn more in our blog here.
Learn More: How Advanced Materials Support Continued Defense Industry Innovation
TriStar is proud to work with a number of defense OEMs to help engineer components for the equipment that helps servicemembers stay safe and effective in their missions. We are excited to engage with projects that intersect with the proud history of U.S. defense manufacturing (like components for the B-52 bomber and vintage P-38 Lightning fighters).
For a deeper dive into the biggest challenges for defense industry components (and how TriStar’s high-performance polymers can help solve them) please see our guide here.