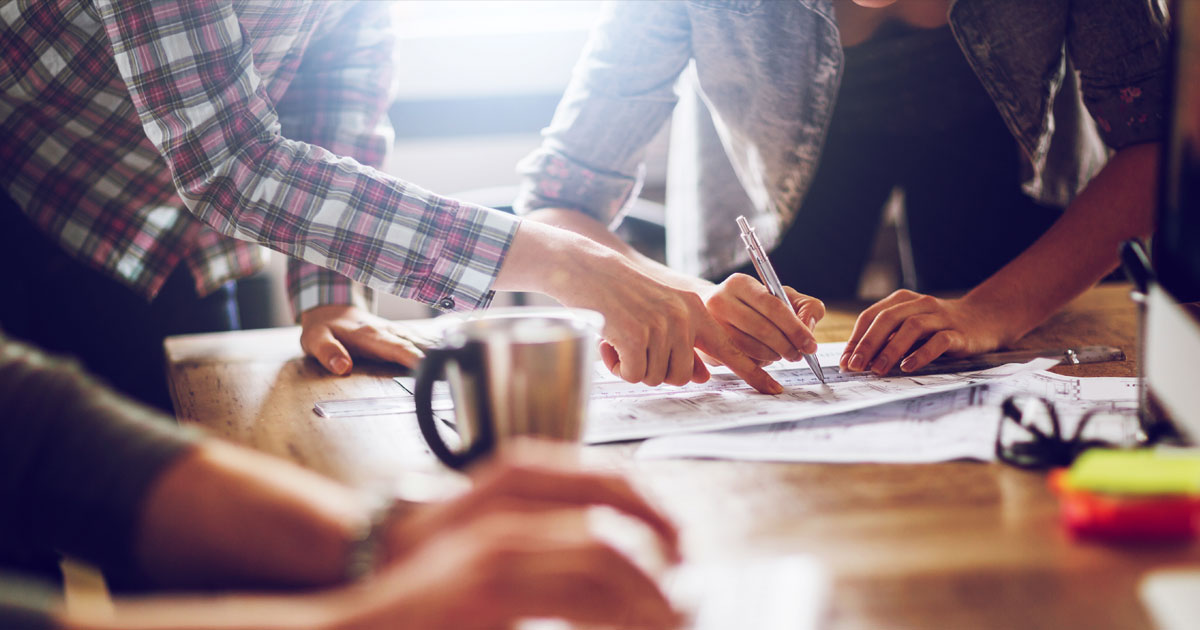
In this blog post, we highlight TriStar’s application-focused approach to finding the right bearing materials for our client’s needs.
For a broader look at bearings, bearings failure, and bearings materials, take a look at our Bearings 101 page here. Or keep reading to learn why choosing the right bearing for an application can be a real engineering challenge.
Careful Component Selection Can Solve Engineering Problems
For fundamental mechanical components like bearings, bushings, and wear pads, material selection matters. Options range from traditional greased metals to advanced, self-lubricating polymers.
Even within a broad material type like polymers, different materials (and material specifications) have very different performance characteristics. These attributes have important implications for the life and effectiveness of the bearing itself. But they can also have much broader effects on the performance of the equipment where they are employed. Excessive vibration, heat, or electrical conductivity can create real problems for the reliability of an entire complex machine.
All too often, however, we see bearings treated like a commodity-part. In this situation, material selection is often based on a broad, pre-existing preference for one material over another. In our experience, this approach comes with real risks. Employing an improper bearing in a design heightens the risk of acute failure. But simply using a sub-optimal bearing may result in chronic problems that affect reliability, maintenance costs, and performance for years without going recognized.
To be clear, there are certainly low-performance, cost-sensitive applications where the priority is simply to find the cheapest possible material. But a wide variety of applications call for materials that are carefully selected to reflect specific operational concerns.
There is no “perfect” bearing material: there’s only the right bearing for the task (and budget) at hand. This reality calls for real engineering expertise to identify the demands of a particular application and match the right material to the application.
TriStar’s Approach: Consultative Engineering to Find the Right Bearing for Every Application
TriStar works with our clients to understand precisely how and where a bearing is going to be used. Our engineers and sales representatives take time to study the applications where our bearings will be expected to perform. In some cases, TriStar team members will spend weeks on-site to learn more about the operating conditions where a bearing or other component will be expected to thrive.
That’s the only way to select materials that are not only fit-for-purpose but capable of solving problems our clients didn’t know they had. For some great examples of this approach in action, see our case study library here.
In some cases, a very subtle problem can result in serious implications for a broader design. Even utilizing a bearing that is over-specified for an application can result in a problem: the bearing may not deform to the intended geometry under operating stress. Within the same factory, and even within the same machine, different bearings may be subjected to very different environmental stresses.
The right materials selection offers a viable solution for many common engineering problems that bearings are called to solve. But to find the right solution, real expertise helps match the chosen material and shape to the precise operating conditions it will be confronting.
The operating concerns listed below illustrate how careful bearing selection is simply good business. A bearing that is marginally cheaper may end up costing far more if it requires frequent replacement or constant re-lubrication.
Example Operating Concerns for Bushing, Bearings, and Wear Pads
- Corrosion: Applications everywhere from manufacturing to underwater introduce corrosion concerns. Even the cleaning chemicals used in food processing plants will destroy the wrong material.
- Dusty and Dirty Environments: Particular matter risks being attracted to traditional grease lubricants almost like a magnet. Once inside the bearing, abrasive contaminants will negatively affect performance and service life.
- Lubrication: inadequate lubrication is the number one cause of bearing failure. The viability and cost-effectiveness of regular lubrication need to be carefully considered when selecting a bearing. Self-lubricating characteristics, for example, are a must in hard-to-reach locations.
- Weight: a lighter bearing capable of handling the same load can offer vital performance advantages for the entire design. For instance, plastic polymer bearings are up to 5x lighter than steel.
- Noise/Vibration: high-levels of bearing vibration is a common operating condition, yet it’s still one of the most common causes of failure for metal bearings. Reducing metal-on-metal contact can help dramatically reduce vibration and noise. This reduction is not only good for the life of bearings but the entire mechanical design.
- Temperature: it’s best to avoid broad generalizations about material temperature tolerances. While every polymer has some theoretical melting point, the right plastics can succeed at relatively high operating temperatures. However, material deformation needs to be carefully considered, as a material can begin losing crucial structural integrity long before its actual melting point.
These concerns are just a few examples, and every different material and application will vary across each of these categories.
At TriStar, we take pride not only in our advanced, high-performance materials but our years of hard-won knowledge on how bearings can be best applied in a huge range of applications.
Our experience allows us to offer our clients a true end-to-end partnership, from solution engineering to final production to support.
From choosing the right polymer to conducting surface treatments to ensure the right adhesion and bonding properties, we treat bearing selection as a real engineering problem that is best addressed with genuine expertise. Our enhanced materials division even adapts our materials to specialized applications such as filtering membranes.
We work closely with clients to understand both functional and financial needs, identifying the material that will ultimately provide the best possible ROI.
For a detailed look at some of our materials and their specific properties, we recommend our materials database here. If you’d like to reach out to our team to discuss finding the right solution for your application, just click the button below.