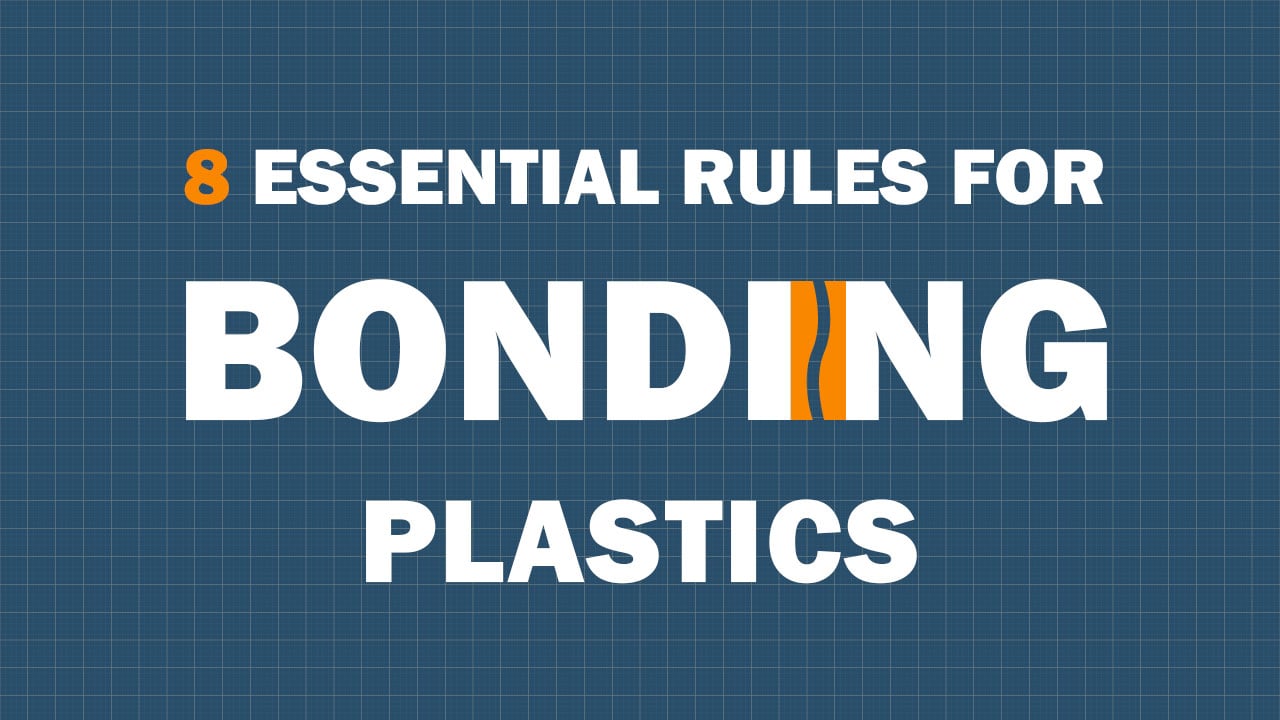
Plastics are an integral part of our daily lives and are widely used in industries such as automotive, aerospace, consumer electronics, medical, and construction. Bonding plastics together can be challenging due to factors like material compatibility, surface energy, thermal expansion, environmental factors, and surface preparation.
In this blog post, we will explore these challenges and provide you with eight essential rules to follow for successful plastic bonding.
Challenges of Bonding Plastics
- Material Compatibility: With numerous types of plastics available, it can be difficult to choose the right bonding method for chemically or physically compatible materials.
- Surface Energy: Plastics typically have surface energies from 18 - 47 with the lower numbers being more difficult to bond. Knowing these differences is critical to understanding how challenging it will be for adhesives to wet out the surface and establish a strong bond.
- Thermal Expansion: Plastics have a higher coefficient of thermal expansion than metals, leading to stress buildup in the bond line and potential adhesive failure over time.
- Environmental Factors: Plastics are sensitive to UV radiation, moisture, and chemicals, which can affect their bonding strength over time.
- Surface Preparation: Proper surface preparation is crucial for strong, long-lasting bonds, as contaminants can hinder adhesion.
8 Essential Rules for Bonding Plastics
- Prepare the substrate and plastic properly via mechanical, primer, or thermal methods to ensure a clean and compatible surface for bonding.
- Clean the substrate thoroughly, even after the initial cleaning, to remove any remaining oil or contamination. Consider using IPA or acetone formulas instead of petroleum-based cleaners.
- Always handle parts with gloves to prevent skin oils from causing bond line failures.
- Check adhesive for compatibility with the plastic. Some adhesives will cause amorphous (see through) plastics to haze and crack.
- Avoid fast-cure adhesives, as they may lead to crystallization and cracking during the cure period. Even those products which are specially designed to cure faster can lead to crystallization and cracking.
- For materials like nylon, acetal, and polyester, consider using a primer first to enhance adhesive bonding.
- When bonding PTFE or PTFE blends (like Rulon®), ensure one side is etched before bonding can begin.
- Optimize joint design to mitigate stress buildup and compensate for thermal expansion differences, using designs like lap joints that distribute stress evenly across the bond line.
By understanding the challenges of bonding plastics and following the eight essential rules, you can achieve strong, long-lasting bonds. If you’d prefer to outsource your bonding process, we’ve got an adhesive system that can bond virtually any plastic to any substrate. This system even eliminates the risk of over-compressing the adhesive. Just ask us for details!
Watch our video (below) for some additional tips.