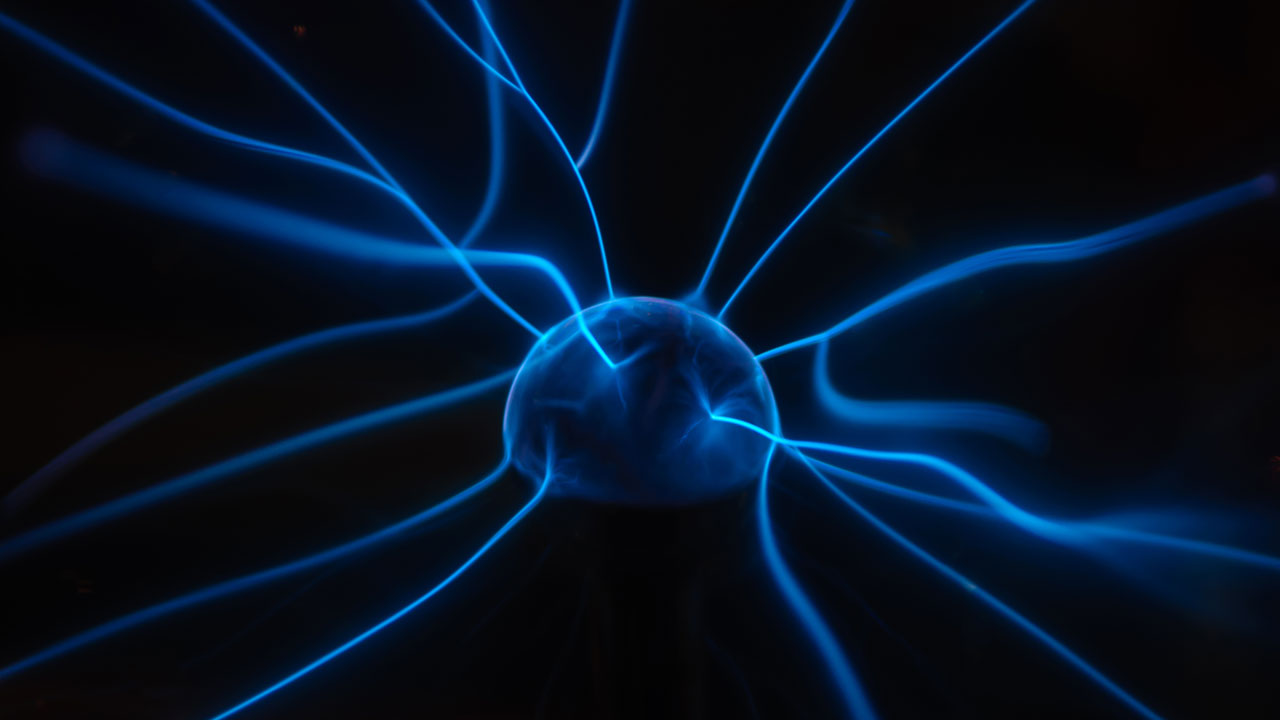
The etching and plasma deposition process is one of the most complex aspects of semiconductor manufacturing. The efficiency and yield of these processes have decisive implications for the economics of semiconductor manufacturing facilities.
For a broader overview of the semiconductor manufacturing process, please see our blog post here. In this post, we take a more focused look at the critical etching and deposition phases of the manufacturing process.
What are plasma etching and deposition?
Plasma etching and deposition are two distinct processes, but because they are so closely interrelated, they are often referred to as the same manufacturing phase. Both are conducted in a vacuum plasma processing chamber using plasma generated from oxygen, argon, or other gases excited by an RF generator.
In short, plasma etching is a form of plasma processing used to manufacture integrated circuits on semiconductor wafers. A plasma discharge is fired in pulses at a target sample, interacting with semiconductor materials and their photolithographed patterns to remove excess material. This highly reactive plasma reacts with surface molecules of isotropic materials like silicon, transforming them into gas which can be removed by the ventilation system of the vacuum chamber.
Plasma deposition refers to “plasma-assisted chemical vapor deposition,” a related process used to deposit thin films onto a semiconductor wafer during the manufacturing process. These films are used to insulate multiple layers of photolithographed structures. In this process, dielectric insulating materials such as Silicon Dioxide (SiO2) and Silicon Nitride (Si3N4) are deposited using plasma. Because plasma directs energy directly onto the surface instead of relying on thermal transfer, deposition can occur at much lower temperatures compared to traditional chemical deposition techniques. This video from Duke University offers a helpful overview of this process.
Key Challenges for the Components Used in Plasma Etching and Deposition Equipment
Certain consumable equipment components, such as screws and wafer handling rings, must function inside the plasma chamber itself. Inside, they are exposed to a variety of challenging requirements including:
- Standing up to temperatures ranging up to 400°
- Avoiding outgassing particles at these high temperatures.
- Exhibiting zero ionic contamination (eg. metals) which could drive defects.
- Possessing strong dielectric insulation properties.
Under these conditions, costly components can wear out quickly, and increasing component lifespan is an important consideration for semiconductor manufacturers. Historically, very few cost-effective polymers have been able to accommodate all of the engineering requirements outlined above. Consequently, Vespel® SP-1 has been a ubiquitous choice in these applications for many years.
Now, however, Meldin® 7001 offers an alternative that provides all of the same critical performance characteristics of Vespel® at an extremely competitive price. In fact, Meldin® exhibits 10-14% better plasma etch resistance compared to Vespel® SP-1. This advantage can lead directly to longer component lifespan, reduced downtime for component replacement, and ultimately higher margins for semiconductor manufacturers employing plasma etching and deposition processes.
For a much deeper look at Meldin® 7001 and the characteristics that enable this polyimide material to thrive in the extreme environment of a vacuum plasma chamber, please see our guide here.