2 min read
What are ‘Fluoropolymers’ and What are their Common Attributes
Dave Biering
June 12, 2018
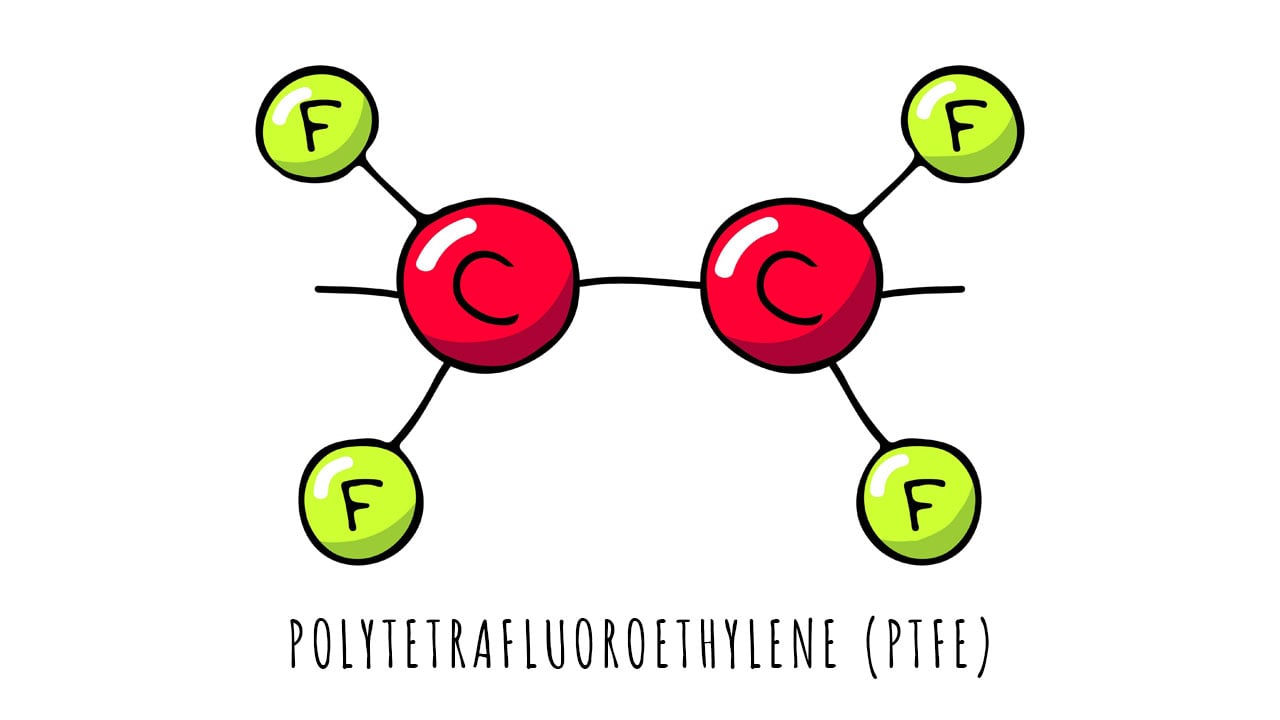
Fluoropolymers are a family of high-performance plastics characterized by their strong carbon-fluorine (C-F) bonds. This unique atomic structure imparts a range of desirable properties, such as chemical resistance, thermal stability, and electrical insulation. They are used in a wide array of industries, including aerospace, automotive, electronics, and medical applications.
The first fluoropolymer, polytetrafluoroethylene (PTFE), better known as Teflon, was discovered accidentally by a scientist at DuPont in 1938. Today, there are several chemical variations based on the C-F structure, which produce a variety of processing and end-use opportunities.
Fluoropolymers can be found in several forms:
- Granulate: The most common form, available as solid granules or pellets. These can be processed using various techniques, such as extrusion or compression molding, to create a wide variety of parts and components.
- Melt-processable: Some fluoropolymers can be melted and processed using techniques like extrusion, injection molding, and blow molding. These melt-processable materials offer more versatility in terms of design and manufacturing, as they can be easily shaped into complex geometries.
- Films: Thin, flexible, and strong fluoropolymer films are suitable for use in applications such as electrical insulation, gaskets, and seals. These films can be produced by various methods, such as casting, extrusion, or skiving.
- Paste: Fluoropolymer emulsion modified paste is a viscous, semi-solid material that can be made into films, thin wall heat-shrink or industrial tubing, pipe seal tape, and membranes. Materials can be sintered or non-sintered depending on the end-use.
- Dispersions: These are liquid suspensions of fluoropolymer particles in a solvent or aqueous medium. These dispersions can be applied as coatings or used for impregnation and are typically used in applications that require a thin, uniform layer of the material.
The specific properties and processing techniques for each type of fluoropolymer can vary based on the chemical composition and formulation. PTFE is the only type that does not melt and is processed through press and sinter techniques, while other common fluoropolymers like FEP, PVDF, PCTFE, and PFA are melt-processible. These processing techniques are critical to the performance of the material in the most difficult applications where heat, chemical exposure, or electrical values are important.
Fluoropolymers have both positive and negative attributes. Positives include being chemically inert (with few exceptions), having broad temperature ranges, low friction, excellent dielectric properties, good thermal insulation, and good wear properties (with certain additives). On the negative side, they can be expensive, have limited processability based on grades, exhibit cold flow with some grades, and have high expansion rates.
This blog post just scratches the surface of the diverse family of fluoropolymers. For a deeper dive into the topic, watch the embedded video (below) or reach out to our technical team with any specific questions you might have.