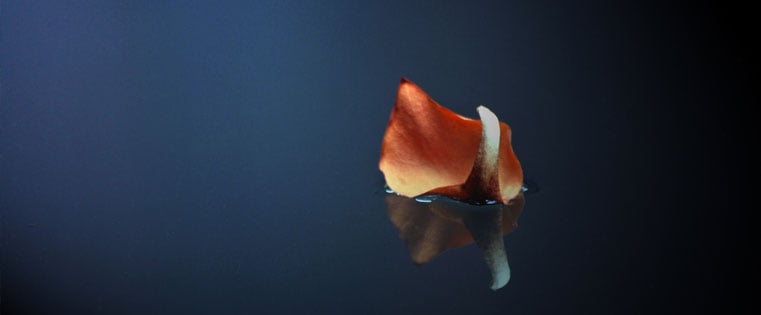
Surface finish is one of the primary considerations in bearing design, since it has a direct impact on the performance of the final product. And achieving the right finish is a careful balance of plastic form vs. plastic function. Consider this:
Is surface finish important? It is, and finish refers to more than just the appearance of the hardware. Ultimately, it relates to how well and how long a bearing will function in your application. When the finish of a shaft is too rough, it will prematurely wear away the plastic bushing. This rate of wear can be compared to having used sandpaper on the component.
If the surface finish is too smooth (such as a mirror finish), the bearing material will not have the right texture to imbed the migratory lubricants. And if the material cannot imbed, the lubricant will not be effective and in fact can raise the coefficient of friction. Increased friction leads to increased wear and now your self lubricating bearing is not living up to it’s potential.
It’s critical to establish the desired finish very early in the bearing design phase to best determine which material to choose, and how to process. The right surface finish and a proper lubrication layer not only reduces friction and wear, but help parts to operate more efficiently and quietly. Explore surface finish in the Bearing Design Technical Paper.
We recently conducted rotary tests using Rulon LR bearings and found that the 8rms mating surface finish had a wear rating of 1, at 16 rms it increased to 1.4, 32 rms 2.2 and at 63 rms 5.3. Roller burnished surfaces performed the best, with ground and polished surface finishes scoring next best. Turned finishes (or mill finishes), tended to have faster wear than the other finishing techniques, even at 16 rms.
As manufacturing becomes more precise, and loads and speeds steadily increase, engineers are paying more attention to the surfaces of bearing design. We’ve got some tips to help you match the right finish to your application in the video below. You’ll also learn how to check a finish using a simple fingernail test.