1 min read
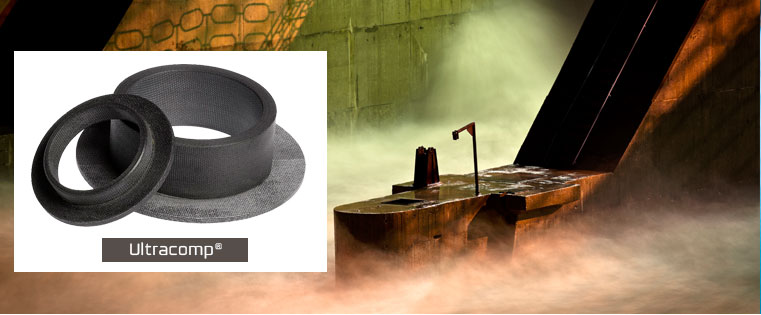
To save time and postage, please sign up for customer paperless invoicing, payments, and vendor payments.
Customers click here
Vendors click here
To request compliance documentation click here.
We had an interesting call on our Ask the Experts line this week concerning underwater bearings and the benefits of wood vs. plastic in a hydro plant application. One surprising fact we reviewed is that like plastic, wood bearings are self-lubricating materials that never require greasing. Yet plastic bearings (such as Ultracomp 300) offer the advantages of dimensional stability in liquids, superior strength, and other benefits reviewed here in our comparison chart.
Wood bearings (also referred to as lignum vitae) are considered an “old-world” bearing material; there’s even evidence showing they were used as rudder bearings by Phoenicians boat builders 4500 year ago! Yet breakthroughs in composites have given plastic the edge in underwater propeller and rudder shafts, switching gear, water turbines, and even petrochemical and wastewater applications. These modern materials resist corrosion, never absorb water and deliver extended service life to help save on replacement costs.
See the differences:
Attributes | Wood Bearings | Ultracomp 300 |
---|---|---|
PV rating | 12,000 | 25,000 |
Max speed | 500 sfpm wet | 100 sfpm dry |
Max load | 1000 psi | 14000 psi dry dynamic |
Max operating temp | -50 to +180F | -375 to +325F |
Friction | 0.07-0.11 | 0.08-0.12 |
Tensile strength | 1,100 psi | 17,500 |
Specific gravity | 1.2 | 1.35 |
Lubricant by weight | 40% | Proprietary |
CTE | 4.3 x 10-6 | 3.3 – 6.24 x 10-5 |
Permanent deformation at 7500 psi load |
.005" | Nil |
After reviewing this information, our caller determined that while wood bearings may still have a place in certain applications, plastic bearings were a superior choice for a hydro plant application. Want to see more technical specifications? Check out our Materials Database.