3 min read
Pulp and Paper Industry History: From Papyrus to Recycled Materials
Dave Biering
November 2, 2021
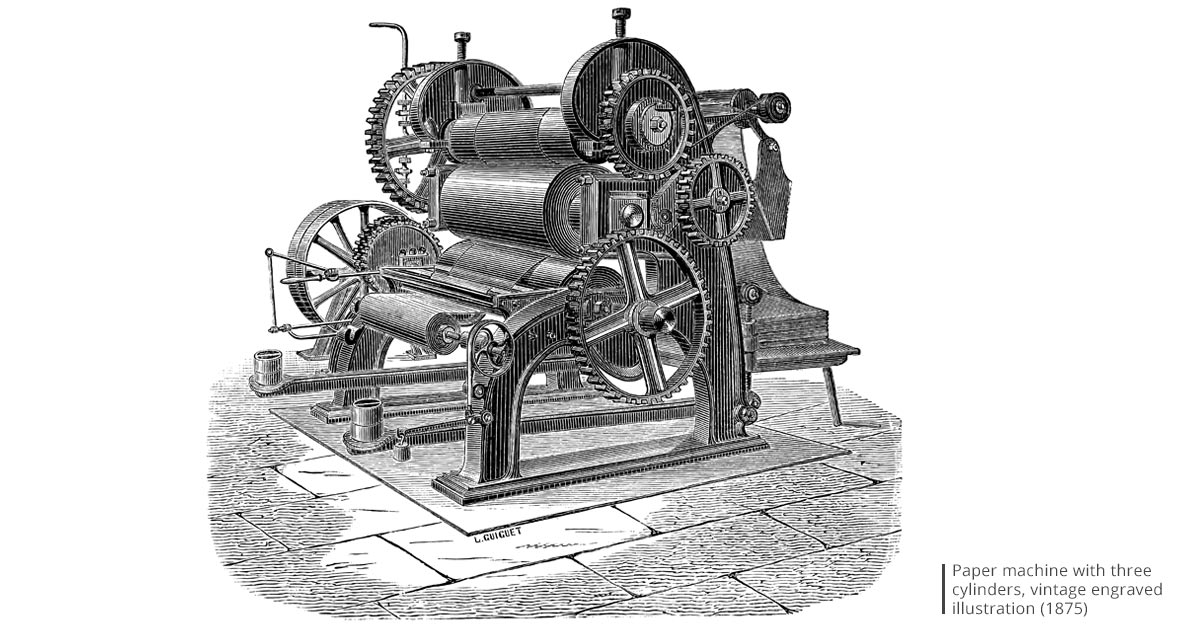
Today, the pulp and paper industry is conducting a historic pivot toward packaging materials, as the digital evolution of work and home life continues to drive reduced usage of traditional graphic paper. (we take a look key industry trends in our blog post here).
This development is just the latest chapter in an industry with a storied history. Humans have been using plant fibers to make valuable materials for writing and beyond since ancient times. In this blog, we provide a brief overview of the history of the pulp and paper industry.
The article below is part of our series examining some of the biggest challenges for pulp and paper equipment manufacturers (and how the right materials can help). For a deep dive on this topic, please see our guide here.
Pulp and Paper Industry History 101: From Papyrus to Chemical Pulping
Paper-making has its roots in ancient Egypt, where thin layers of papyrus plant were used to form sheets, and then stacked on top of each other at right angles and pounded together. In fact, our modern word paper comes from “Papyrus” (which means paper-reed in Latin).
Papyrus was tough and constituted (aside from wet clay) the world’s first mass-produced writing surface. Unlike true paper, however, papyrus was made from plant fibers that have not been broken down. It has rough edges and surface, and the underlying strips can begin to separate when used repeatedly.
True paper was first created in China, with evidence of the first paper making dating from around the 1st century BC. Early Chinese paper was most often made using tree barks. In China (as would be the case in Europe several centuries later) the birth of printing transformed the paper market. Without the restriction of handwriting, the scale of written media exploded. So did the demand for paper, and inputs like bark could no longer be collected in sufficient quantity. New techniques were pioneered for making pulp from hemp, flax, cotton, and old rags/ropes (at this time, raw wood chips still could not be effectively processed).
In essence, though conducted through manual labor, these early paper-making processes were similar to paper manufacturing today. A fibrous pulp was made, drained, and air dried before being pressed and cut into sheets.
These paper-making processes spread their way across Asia and then to the Islamic world (which, like Europe at this time, used parchment made from animal skins). Paper was much more cost effective than parchment and spread as quickly as new civilizations acquired the knowledge needed to manufacture it. In the Middle East, animal- and water-powered mills emerged that allowed for truly bulk paper manufacturing for the first time. This knowledge soon made its way to Europe through Islamic Spain, and by the late Middle Ages paper mills were operating in Spain, France Germany, and Italy.
Around 1799, the Fourdrinier Machine enabled continuous paper-making for the first time. Until this device, paper had to be pressed and dried one sheet at a time. Originally developed in England by the French Fourdrinier brothers, this basic design has become so commonplace (with some evolution) that these machines are now often simply called “paper machines.” It uses a conveyor belt, traditionally made of wire mesh, to continuously drain water from paper as it moves down the line.
The introduction of wood pulp processing in 1843 allowed papermaking to move beyond a reliance on used textile products. Until then, paper mills had resorted to employing “rag-pickers” to comb streets and garbage heaps for scraps that could be processed into paper.
The use of wood chips was the final ingredient needed to make paper a relatively inexpensive good for the first time. And modern society would come to “run on paper” for the next century and a half. Just as it had with the invention of printing, new tools like mass produced pencils and fountain pens would create a whole market for paper. And at cheaper prices, modern realities like school textbooks became widely possible for the first time.
The engineers of the pulp and paper industry would continue to develop new methods for making new products (like cardboard and other packaging materials), increasing yield, and handling new inputs (like recycled materials). We look at today’s prototypical process, including key types of equipment, in our blog post here.
Learn About Key Challenges for Pulp and Paper Equipment Manufacturers
Today’s pulp and paper OEM’s continue to push boundaries by engineering solutions capable of working more efficiently, withstanding more caustic processing chemicals, and minimizing unplanned downtime.
Doing so is rarely easy. The pulp and paper industry exhibits some of the most challenging manufacturing environments around. Critical components needs to be ready for chronic exposure to water, both end of the pH scale, abrasive wood chips/paper dust, and more (often, one or more of these complicating factors is present at the same time)
TriStar has worked with a number of pulp and paper equipment manufacturers to help match our advanced materials to use cases where they directly address some of these operational challenges. Pulp and paper industry applications are typically best served by carefully engineering materials and components to reflect specific operating challenges.
We take a deeper look at some of these challenges in our in-depth guide here (also available as a free whitepaper for offline reading):