Pulp and Paper Equipment Manufacturers’ Guide to Polymer Components
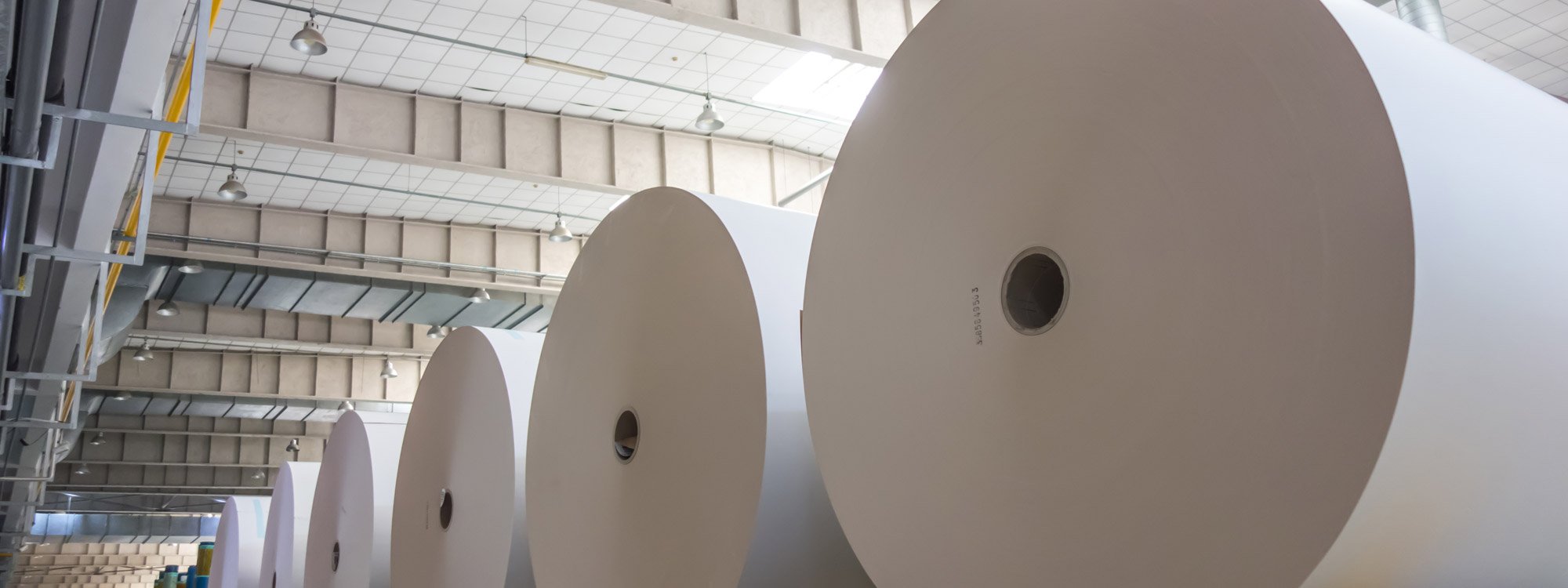
The pulp and paper industry comprises over 450 mills across North America, over 4% of US manufacturing GDP, and over 475,000 jobs across the US and Canada.
The industry is a vital cog in the economy, and at each stage in the production process, specialized equipment plays a vital role. This equipment is expected to handle the complex process of turning wood chips into a variety of salable products like paper.
This industry is relatively decentralized, with many independent paper mills thriving alongside larger enterprise operations. Combined with the huge variety of wood inputs, this diversity translates to a never-ending variety of use cases for pulp and paper equipment, non-standard operating parameters, and an incredibly complicated challenge for OEM’s.
TriStar has worked with a variety of pulp and paper industry OEM’s, and we have seen up close how challenging this industry can be. Our team distilled some of this practical experience into the guide below.
Prefer to read this later? We'll email you a PDF.
Industry Overview: A Varied Market for Pulp and Paper Equipment Manufacturers
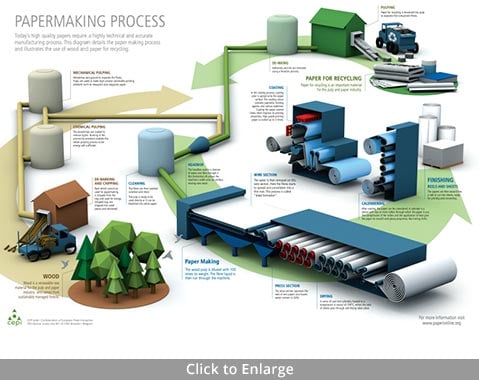
Paper mills’ basic task is to covert raw wood chips into pulp, which can then be further processed into a variety of different products. The list below provides a basic overview of this overall process. For a deeper look, this video provides a great look at the process in action.
- Trees are debarked and processed into raw chips. Raw inputs must be cleaned and filtered for contaminants like stone and metal scrap.
- Wood chips are processed into “pulp,” a material created by separating the cellulose fibers from wood (or other sources like fiber crops or recycled materials). Pulp can be processed either chemically, mechanically, or using some combination of both approaches.
- Pulp is refined and treated with a variety of processing chemicals to make slurry.
- The slurry is filtered through a series of screens (the precise engineering of this screens can vary widely) and water is gravity- or vacuum-drained.
- Water paper sheets are pressed, dried, and finally processed into final products like:
- Various grades of consumer and commercial paper.
- Paperboard
- Packaging
This work is complicated by the fact that the industry’s main input—wood—is so variable. Every geography features different wood types, costs, and different product demand. And wood varies widely not only in type, but quality. Irregularities ranging from bullets to metal posts (known within the industry as "tramp metal") are known to be found in the wood processed at paper mills. Other facilities specialize in processing recycled products like newspaper or old packaging material, adding even more variation to the mix.
These heterogeneous inputs, combined with the number of successful smaller firms in the industry, mean the pulp and paper industry has a uniquely diverse number of approaches to getting the job done. While the process above is prototypical, there are endless variations to how these basic tasks are accomplished.
Mill-to-mill variation creates complexity for OEM’s, who must find a way to support equipment not always operated “by-the-book.”
In this high-volume industry, margin matters, and even a few hours of downtime can represent $100,000+ in costs. In this context, keeping equipment operating reliably is a vital business requirement. But, in a highly challenging processing environment featuring myriad environmental threats to equipment components, doing so is rarely easy. Fortunately, the right materials can help OEM’s deliver products that perform even in tough conditions—provided they are carefully engineered to the task at hand.
Finally, US pulp and paper companies are often pushing technological boundaries, using more aggressive thermo- and chemical processing to achieve enhanced yield and output, and the right materials are instrumental in accommodating even more extreme conditions. More aggressive processing also allows for upstream savings, as cleaning and filtering for contaminant can be reduced with stronger processing capabilities. In many regions, water conservation is an increasingly salient issue, and more aggressive heat and chemical use can also help limit the need for washing with huge quantities of water.
What Makes the Pulp and Paper Industry Such a Challenging Engineering Environment for Pulp and Paper Equipment Manufacturers?
Not all pulp and paper processes are created equal. Different woods require different processing approaches. And many mills put their own spin on the process, always seeking any tweak that can maximize output and yield.
While precise methods are varied, they tend to share the same cluster of engineering challenges. Processes requiring caustic chemicals in combination with higher operating temperatures present the single toughest nut to crack. As you will see below, however, these chemicals are just one aspect of this challenging environment. Any of the issues discussed below can create problems if not properly for taken into consideration during the material and component selection processes.
Fortunately, TriStar’s experience suggests that each of these challenges can be successfully addressed with advanced materials if they are carefully chosen to reflect specific operational challenges.
Pulp and Paper Industry Equipment Challenge One: An Industry Defined by Abrasive Media
As we explore in other industry pages, even material like grain dust can be become highly abrasive, especially when it works its way deep into complex mechanisms. In the pulp and paper industry, this issue is even more salient: wood and wood biproducts are extremely abrasive by nature. Rocks, clay, dirt and "tramp metals" are often included with raw wood material, adding even more abrasive content to the slurry. Paper dust is also inherently abrasive.
All of these problems cause excess wear on components like bearings while degrading surfaces and mating components. Abrasion becomes even worse when abrasive particles become stuck in mechanical lubricant, creating a lapping compound that exponentially amplifies wear.
Pulp and Paper Industry Equipment Challenge Two: Caustic Chemicals
Caustic chemicals are everywhere in pulp and paper applications and represent a constant risk to any components using the wrong materials. Common pulp and paper chemicals cover a wide swath of the pH scale, further complicating material sourcing. They include:
- White Liquor: a hot mixture of Sodium Hydroxide and Sodium Sulfide.
- Black Liquor: the by-product from the kraft process when digesting pulpwood into paper pulp removing lignin, hemicelluloses, and other extractives from the wood to free the cellulose fibers used in paper-making.
- Bleach: used to whiten paper.
In general, this caustic environment compels pulp and paper OEM’s to utilize relatively high-cost metals and alloys to mitigate corrosion wherever possible.
Pulp and Paper Industry Equipment Challenge Three: Huge Volumes of Water
Water is used in huge volumes to rinse raw wood, process pulp, and move material down the line. This usage creates a twofold challenges for companies in the industry. First, more and more facilities are under pressure to limit water use (particularly in regions with more sharply limited water supplies). Second, wet environments can cause lubrication to migrate into the system, which can risk contaminating slurry.
Pulp and Paper Industry Equipment Challenge Four: Noise, Vibration, and Static Buildup
Pulp and paper processing is heavy duty work full of metal-on-metal contact which creates noise pollution, vibration, and static buildup. These issues are only amplified as the overall speed of production is increased. A variety of motors, conveyors, and other processing equipment create high-level of vibration which can risk damaging equipment, decrease efficiency, and even risk occupational safety hazards if a part breaks loose and enters the system.
How the Right Materials Can Help Pulp and Paper Equipment Manufacturers Deliver Better Products Than Ever
The challenges above can be “more difficult than the sum of their parts.” Finding a cost-effective component material to address any one of the challenges above isn’t easy. Sourcing one that can support an environment like the pulp and paper industry, where all of these issues can be present at the same plant, is much harder still. A top material for heat-resistance, for example, will not necessarily be abrasion resistant. A component might perform great in the face of caustic chemicals but degrade in the face of ozonated water (which destroys PEEK).
The diversity of operators and methodologies in pulp and paper creates another issue. In this largely decentralized industry, the same terminology is often used to describe certain broad categories of processes or equipment, despite major differences in crucial application parameters. Without careful attention to the application (and operating environment) at hand, materials can easily be underspecified. Therefore, it is extremely important to review each application thoroughly to verify operating conditions/process specifications.
That’s precisely why we recommend an engineering-driven approach to component selection (we explore this topic in a little more depth here. It can be easy to treat components like bearings as a commodity to be sourced from the cheapest bidder. These components, however, play a crucial role extending the lifespan of equipment expected to perform in tough operating conditions, with minimal downtime, for years (or even decades). In this context, we find it almost always pays off to focus on the true lifecycle cost of key components like bearings.
A part that costs more upfront can drive substantial lifecycle savings if it lasts longer, avoid unplanned downtime, and enables more aggressive processing.
In other cases, however, TriStar has been able to use our advanced material expertise to tackle urgent engineering challenges while achieving direct cost savings.
Mini Case Study: Reducing Screen Costs for a Pulp and Paper Equipment Manufacturer
Challenge:
TriStar worked with a pulp and paper industry client which employed various filter screens made from 316 stainless steel mesh. One dual machine employs 500+ screens, costing several hundred thousand dollars to replace the full set of screens.
Though each screen is designed to last 8-10 years, the sheer scale of this application was driving up costs. Every screen replacement represented not only direct cost, but costly downtime. The client reached out to TriStar for help finding a material that could last longer while staying cost competitive with stainless steel.
Solution:
The right component would need to be stable under operating temperature 90-100 degrees Fahrenheit, be quickly replaceable, and offer a wide range of chemical resistance.
Using our advanced polymers, TriStar fabricated a prototype that performed well in initial trials, and we proceeded to source the part for injection molding.
This solution flew far under the client’s target price of $250 per unit—TriStar was able to source these injection molded parts for around $11 each.
Key Capabilities of TriStar Materials for Pulp and Paper Equipment Manufacturers
TriStar has extensive experience engineering our materials for bearings and other components in pulp and paper industry applications. While there is no single perfect material, our deep arsenal of options gives us the depth of solutions needed to match precisely the right capabilities tos each and every use case.
- In addition to offering strong abrasion resistance, TriStar materials can actually embed particulate matter in the surface of a bearing or other component. This approach helps reduce abrasive contaminants deep inside complex processing equipment, a great example where the right material can protect not only a component, but the machinery around it.
- TriStar materials offer excellent resistance to caustic chemicals. Crucially, we offer materials well suited to the full breadth of the pH scale found in pulp and paper industry applications.
- Different TriStar materials tolerate the temperature ranges required by pulp and paper applications. There are a number of options for high temperature materials, but much fewer that also support the other capabilities in this list—TriStar’s advanced polymers can be engineered to offer the best of both worlds.
- Self-lubricating polymers (you can learn more about how this works in our video here) offer several crucial advantages in the pulp and paper environment. Eliminating grease helps reduce sticking to particulate matter, lessen the risk of lubricant-contaminated slurry, and dramatically simplifies maintenance (which directly reduce support costs while also minimizing downtime).
- We offer low-moisture absorption materials that are well-suited to machinery where a component may very well be wet near 24-7.
- Self-lubricating polymers protect mating components (shafts, housings, wear plates), many of which are made from costly high-performance metals, from damage - resulting in significant cost savings.
- TriStar's Polymers and Composites effectively reduce dust/airbone particulates and noise throughout the mill.
- New antistatic and static dissipative plastics are extremely effective in reducing static electricity to
protect sensitive equipment throughout the mill.
Collectively, these features add up to a deep well of options for component materials capable of supporting better performance, longer part life, and enhanced reliability. Our solutions have been used across the full pulp and paper production chain, from material handling and initial processing, to pulping, to specialized support equipment, to final product processing (drying/finishing/converting).
Below, we take a look at some prototypical TriStar pulp and paper solutions. For a deeper look at our full list of materials offerings and their specifications, please refer to our interactive materials database here.
TriStar Materials for Materials Handling Equipment and Wood/Chip Processing Equipment
While this equipment doesn’t involve the same levels of caustic chemicals or water as pulping, it can still present some difficulties.
In both plane and rolling bearing applications, TriStar’s Rulon and CJ composite materials have proved to be excellent alternatives to traditional options like brass, bronze, or lead. Our materials provide attractive mechanical properties like lower friction and reduced noise compared to metal components.
In other wood chip use cases, our Ultracomp material (well suited for high load, low-speed applications) is a great fit for both linear and rotary bearings, friction plates, and rollers. Our Trilon specialty polyolefins have been successful used as conveyor bearings, rails, shoots, slideways, and chain guides—where they can help dissipate static and reduce metal-on-metal contact. We even offer specialty metal-detectable polymers, which can be detected with standard metal detection equipment for filtering, etc.
TriStar Materials for Pulping Equipment
Paper pulping is one of the challenging environments for equipment in any industry, but TriStar materials have proven to be up to the task. The right material for the job will depend on the temperature being utilized in a precise application, with the full lineup of Rulon, Ultraflon, CJ and FCJ offering valuable options at a number of different specifications.
In addition to functioning well in the components discussed above under Wood Chip/Processing equipment, our materials also thrive when used in seals and bearing seals (as an alternative to not only metals, but elastomers). Our pulping components offer low moisture absorption, embed particulate matter, and can resist highly caustic chemicals. Increased component tolerances can not only enhance uptime and reliability, but potentially alleviate mechanical constraints on the intensity of the process being employed.
TriStar Materials for Drying, Finishing, and Converting Equipment
Once the pulping process is complete, a few more challenges remain before paper products are “out of the woods”. The drying/finishing/converting process involves elevated temperatures that have traditionally required high-cost metals. At this stage, paper dust also becomes a significant issue—especially if it becomes embedded in sticky grease. Once again, TriStar materials provide the perfect solution.
Learning More About Advanced Polymers for Pulp and Paper Equipment Manufacturers
We hope this page has provided a valuable overview of why the right materials are essential for addressing some of the foremost engineering challenges for pulp and paper OEM’s.
The TriStar team is passionate about learning the ins and outs of every client’s industry. There’s no substitute for ground-level knowledge of applications and operational challenges, and a commitment to not just selling advanced materials and components but engineering them to solve chronic business problems. In our experience working with a variety of pulp and paper enterprises across North America, this consultative engineering approach almost always pays off.
This vision for our engineered polymers is rooted in our belief that material selection matters. In many cases, the right materials can not only increase component lifespan and reduce failures but solve problems that OEM’s didn’t even know they had. Issues like excessive vibration or leaking grease can create systemic issues that are not confined to a single component. Instead of treating bearings and other components as a commodity to be sourced from the cheaper bidder, they should be approached as vital contributors to the value of an overall equipment design.
Because we don’t focus on bulk orders, no client’s business challenge is too low volume for our team’s attention. TriStar takes pride in providing the same level of service to businesses of all sizes, which is especially important for the many smaller independent OEMs in pulp and paper.
Frequently Asked Questions
Here are a few common questions relating to the content in this guide.
Q: What makes the pulp and paper industry so challenging for bearings?
A: Bearings must withstand abrasive “tramp metal,” caustic chemicals, high water use, noise, vibration, and static buildup in pulp mills. Components face diverse wood inputs, chemical ranges, and constant moisture. TriStar’s materials are engineered to meet these combined challenges.
Q: How do TriStar materials resist caustic chemical exposure?
A: TriStar offers materials well-suited to the full pH range, providing excellent resistance to caustic chemicals found throughout pulp and paper processes.
Q: Why are self-lubricating polymers beneficial in pulp mills?
A: Self-lubricating polymers eliminate grease, reducing particulate buildup, slurry contamination, and maintenance needs, simplifying upkeep in wet, abrasive environments.
Q: Do TriStar materials handle moisture effectively?
A: Yes. They offer low‑moisture absorption, ideal for machinery operating wet almost continuously, preventing degradation from water exposure.
Q: Can TriStar's materials reduce mill noise and dust?
A: Their polymers and composites reduce airborne particulates, dust, and static/dissipative noise throughout the mill, boosting performance and operability.
Q: What bearing materials are best for high-load, low-speed conditions?
A: Ultracomp is designed for high-load, low-speed scenarios like rollers and friction plates, while Rulon and CJ composites offer low friction and noise reduction.
Q: Are TriStar materials suitable for seals used during pulping?
A: Yes. Their materials thrive in pulping seals—they resist highly caustic chemicals, absorb minimal moisture, and embed particulates to protect other components.
Q: How do TriStar materials improve lifecycle performance?
A: By addressing abrasive wear, chemical exposure, moisture, static, and noise simultaneously, TriStar delivers components with longer life, improved reliability, and future-proof performance.
Q: What specialty polymers does TriStar offer for conveyor and guide systems?
A: Trilon specialty polyolefins are used for conveyor bearings, rails, slideways, and chain guides—and help dissipate static along equipment pathways.
Q: How many pulp and paper mills are there in North America, and how does TriStar support them?
A: There are over 450 pulp and paper mills across North America. TriStar supports this sector with tailored polymer bearing and wear solutions for each process stage—helping reduce maintenance, resist harsh chemicals, and extend component life in challenging mill environments.