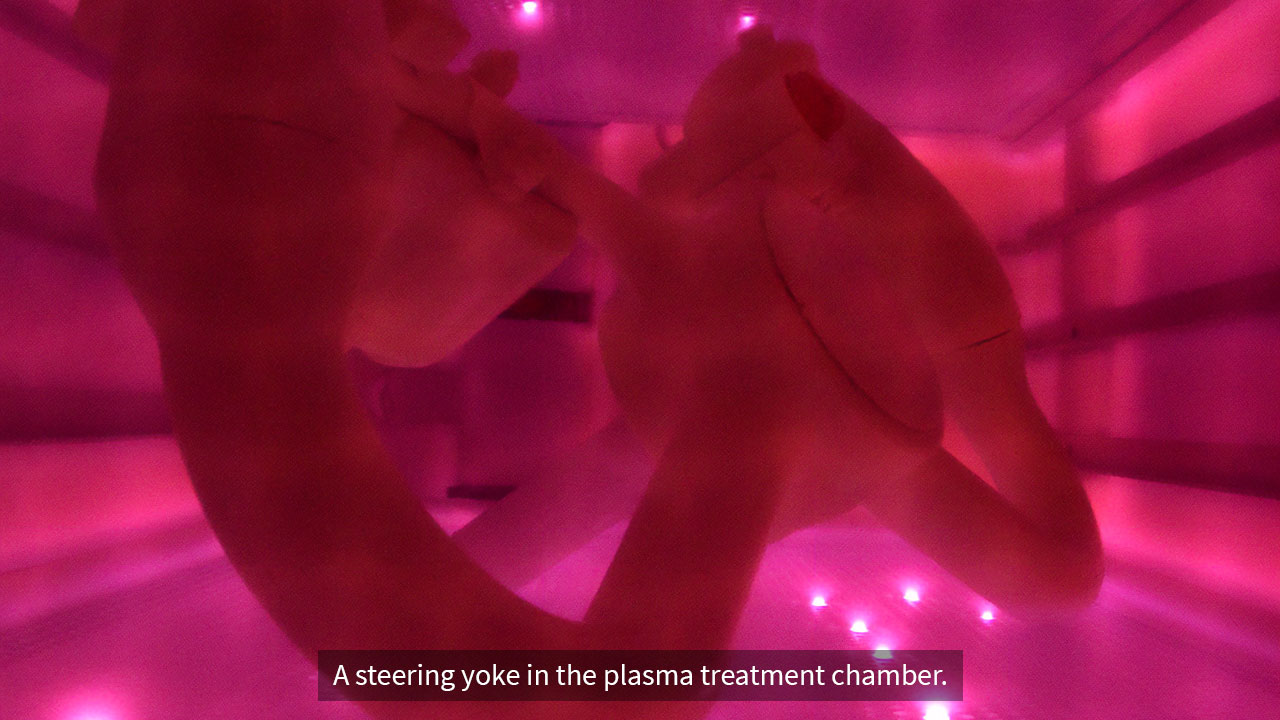
Cleaning can be a critical first step in many manufacturing processes, particularly for the medical, aerospace, and electronics industries. Proper cleaning ensures that surfaces are free from contaminants, providing an adherent surface on the mating materials. In this post, we will discuss the benefits and drawbacks of two popular treatment methods: dry (plasma) and wet (aqueous) processes.
Where Should I Use Plasma Cleaning?
Plasma surface treatment is ideal for applications requiring absolute cleanliness and highly active surfaces. For example, medical or optical devices requiring specialized coatings or sensors that require potting perfection in electronic components. Plasma cleaning and activation are for products that require high precision, high yield, and extremely low failure rates.
Dry Plasma Cleaning: The Process and Benefits
Dry plasma cleaning is a non-abrasive, solvent-free process that utilizes ionized gas, or plasma, to remove contaminants from surfaces. The process is performed in a vacuum chamber and gases such as oxygen, argon, or nitrogen are ionized to create the energized cloud that envelops the device for a complete surface atomic interaction.
Advantages of Dry Plasma Cleaning:
- Truly Clean Base Surface: Plasma cleaning removes all traces of contamination, including the residues that wet cleaning methods leave behind, providing an ideal, hydrophilic base surface for enhanced bonding and other processing steps (e.g., printing, painting, coating, potting).
- Uniform 3-D Coverage: The dry plasma cleaning process can cover the entire substrate, even complex geometries, ensuring a consistent clean.
- No Impact on Dimensional Tolerance: Plasma cleaning does not affect the dimensional tolerance of components, making it suitable for applications where maintaining the initial specs are critical.
- Efficient Cleaning of Microscale Features: Plasma cleaning can effectively clean surfaces with microscale porosity or microchannels, which are not suitable for solvent cleaning due to surface tension limitations. This makes it ideal for applications in microelectronics, medical devices, and other industries with intricate structures.
- Environmentally Friendly: Dry plasma cleaning is an eco-friendly process as it does not generate hazardous waste or consume large amounts of water.
Disadvantages of Dry Plasma Cleaning Processes
Size constraints are a disadvantage. Plasma cleaning is typically done in a vacuum chamber. Therefore, the size of the parts should be smaller than a bread box. Otherwise, a custom chamber will need to be built.
Wet Cleaning Processes: The Basics and Advantages
Wet cleaning processes involve the use of liquid solvents, detergents, or cleaning agents to remove contaminants from surfaces. These processes can be categorized into immersion, spray, or ultrasonic cleaning techniques, depending on the method used to deliver the cleaning solution to the target surface.
Advantages of Wet Cleaning Processes:
- Effectiveness: Wet cleaning processes are highly effective at removing a wide range of contaminants, including oils, greases, and particulate matter.
- Cost-Effective: The cost of wet cleaning processes is generally lower than that of dry plasma cleaning, making it more accessible for smaller businesses and budget-conscious operations.
- Familiarity: Wet cleaning processes have been widely used for many years, so there is an abundance of knowledge and experience in their application.
- Scalability: Wet cleaning processes can be easily scaled up or down to accommodate various production volumes.
Disadvantages of Wet Cleaning Processes
Many environmental regulations have restricted certain chemicals and solvents from being used, leaving either green cleaning solutions or plasma as the only options.
Comparing Dry Plasma Cleaning and Wet Cleaning Processes
To determine which cleaning process is best for your needs, it's essential to consider the specific requirements of your application, such as the materials involved, the type of contaminants to be removed, and any environmental or budget constraints. Here is a summary of their key differences:
- Material Compatibility: While both methods are versatile, dry plasma cleaning is generally more compatible with a broader range of materials, including sensitive substrates.
- Precision and Control: Dry plasma cleaning offers greater precision and control in the cleaning process, while wet cleaning processes can be more aggressive and may require additional steps to ensure optimal results.
- Environmental Impact: Dry plasma cleaning is more eco-friendly than wet cleaning processes, as it does not generate hazardous waste or consume large amounts of water.
- Residues: Wet cleaning processes may leave behind residues that can impede bonding, while dry plasma cleaning ensures a residue-free surface.
The choice between dry plasma and wet cleaning processes ultimately depends on your specific needs, requirements, and constraints. While dry plasma cleaning offers superior precision, compatibility with a broad range of materials, and an environmentally friendly process, wet cleaning processes can be more cost-effective and easily scalable. To learn more about plasma cleaning services and determine the best solution for your application, we invite you to contact our surface modification experts who can guide you through the process and help you achieve optimal results.