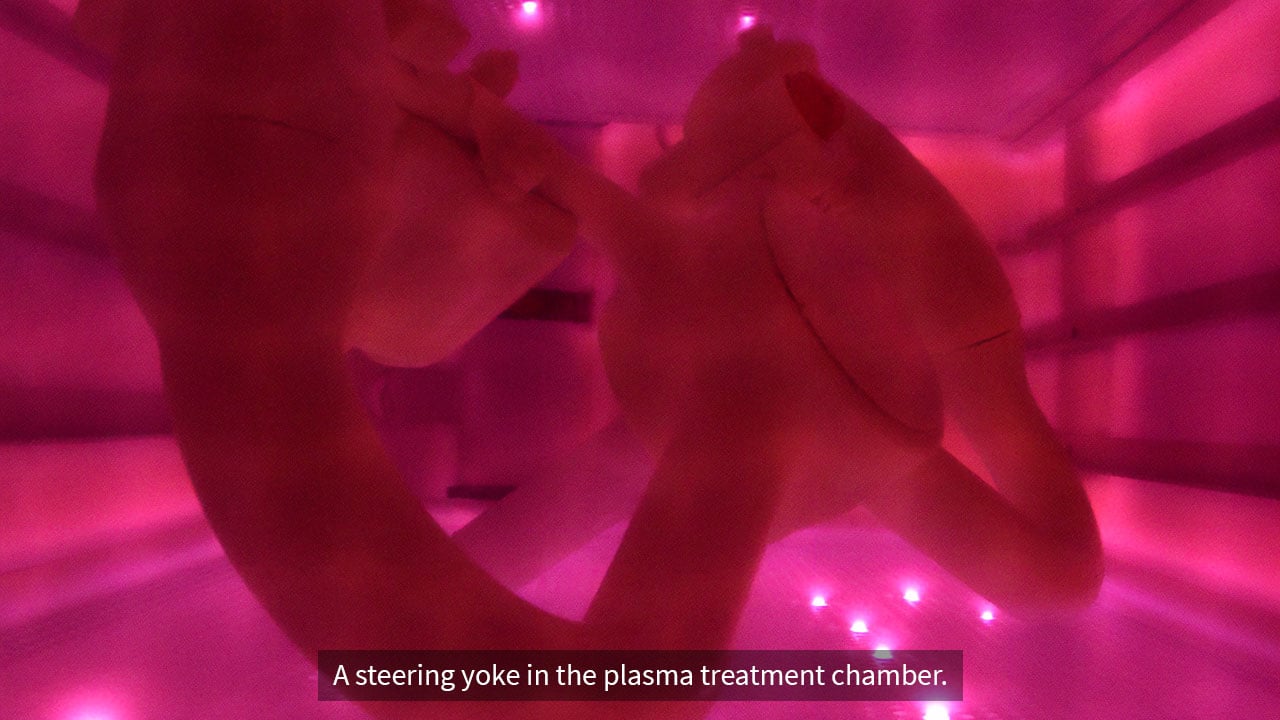
3 min read
Cleaning Process Review: Plasma vs. Aqueous
Cleaning can be a critical first step in many manufacturing processes, particularly for the medical, aerospace, and electronics industries. Proper cleaning ensures that surfaces are free from contaminants, providing an adherent surface on the mating...
Read More