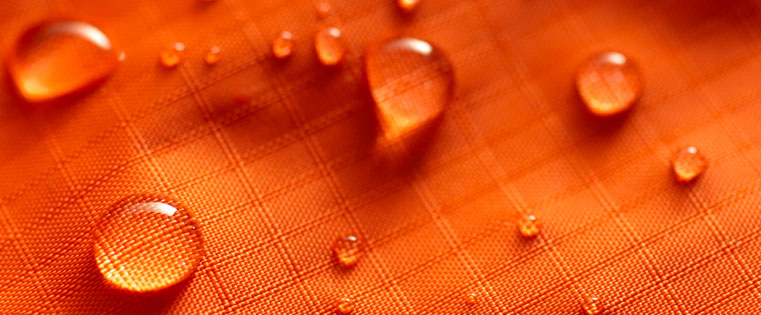
There is usually a good correlation between bonding and wetting. Wettability can be defined as “the ability of a solid surface to reduce the surface tension of a liquid in contact with it such that it spreads over the surface and wets it.”
So, it seems intuitive that good wetting would automatically result in strong bonds. However, this is not always the case. Two different cases where this correlation can break down are:
- Case #1 - Where the surface is wettable but the structure beneath (the "bulk property" of the material) is too weak to have good bond strength.
- Case #2 - Where the surface is not wettable by water but there is still excellent bonding.
In this post, we will explore two examples of the first case: the bonding of PTFE (Teflon®) and the bonding of a waxy or oily surface.
Example #1 – Poor Bonding due to Inherent PTFE Surface Weakness
Polytetrafluoroethylene (PTFE) can be plasma treated to promote good wetting by water or adhesives; however, when the surface is bonded, the measured bond-strength is about half to three-quarters of that obtained by using a commercially acquired sodium etchant. The reason is that the surface structure of PTFE is very weak due to almost no cross-linking within the material composition. The top layer of the polymer will shear off with the adhesive, even if the surface is treated with plasma to give good and uniform wetting.
To get good bond-strengths between PTFE and an adhesive, it is necessary to use a surface treatment that cross-links to a significant depth within the polymer (usually 1 micron or more), such as the aforementioned sodium etching method. Plasma treatments generally only affect the top 0.01 microns of the material, so the resulting surface treatment is just not thick enough to give a strong bond even though it is wettable and bondable by the adhesive.
Example #2 – Poor Bonding Due to Oily/Waxy Contamination Layer
As a second example of a weak surface layer; it is easy to plasma-treat a waxy or oily surface and make it completely wettable and bondable by adhesives. However, these bonds will show almost no strength because the adhesive is not bonded to the substrate - only the surface contamination layer. This is the ultimate example of a weak boundary layer. It is also the primary fault of using a "wetting test" as the sole quality control test for plasma treatments. The apparent surface of the part may be completely wettable but still give very poor bonding because that surface is really a layer of cross-linked contaminate.
The Bottom Line
These are examples of scenarios where plasma treatment is not the best approach for improving bondability; there are many other situations where it is appropriate. The key is to partner with engineers with the expertise to use the best method for your specific situation. Let us know what you are dealing with, and we’ll let you know how best to proceed!