Using Enhanced Materials to Solve Tough Engineering Problems
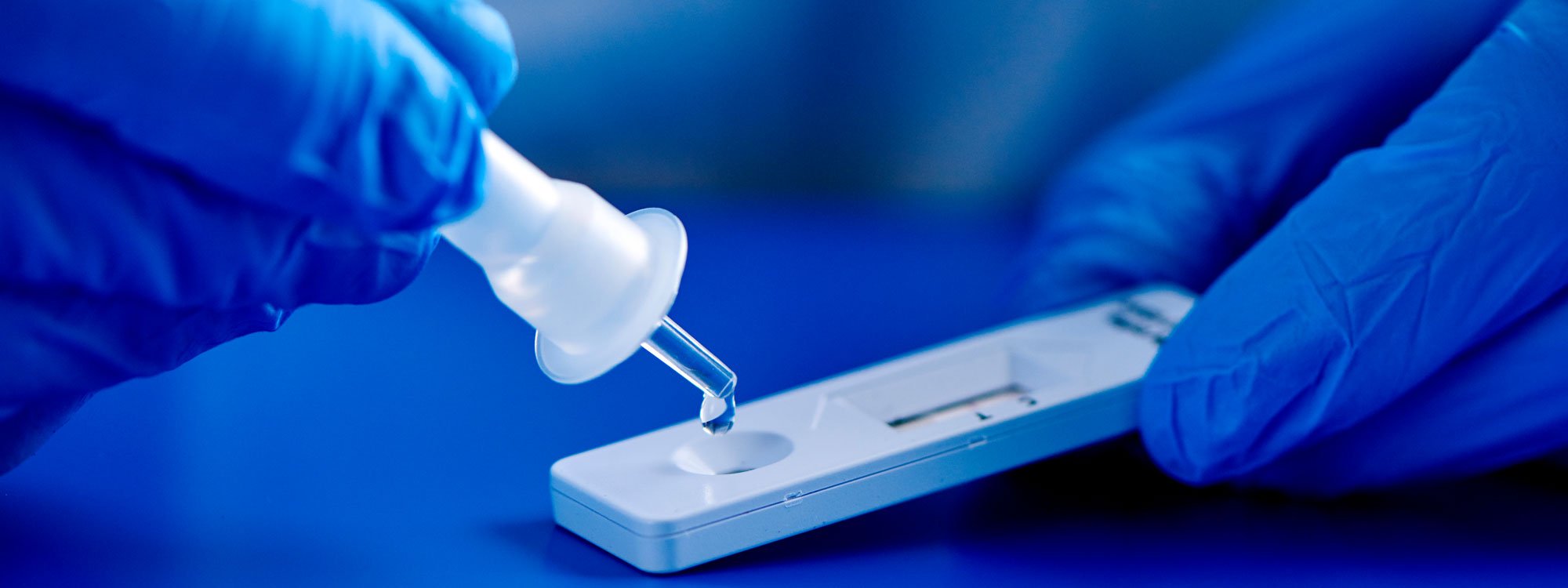
How can manufacturers enhance their materials to have the desired functional properties?
Advanced techniques like plasma surface modification offer a powerful option. But harnessing these techniques requires specialized engineering knowledge that many organizations do not possess in house. TriStar’s Enhanced Materials Division (EMD) provides a solution.
By combining advanced materials modification capabilities with high-touch consultative engineering, TriStar’s enhanced materials team offers a one-stop shop for getting the most possible performance out of critical materials.
EMD effectively works as an auxiliary engineering team for TriStar clients, working directly with client engineers and product development teams to solve tough materials engineering problems.
Prefer to read this later? We'll email you a PDF.
What is the Enhanced Materials Division?
TriStar Enhanced Materials Division offers clients a one-stop shop for solving tough engineering challenges. From material selection, to advanced surface enhancement, to in-depth consultative problem solving, EMD can identify cost effective solutions geared to unique project requirements.
For a comprehensive listing of EMD’s product offerings and services, please see our data sheet here. At a high level, EMD capabilities cover:
- Surface Enhancements, including plasma treatments, specialized coatings, parylene, and primers.
- Advanced Product Offerings, including adhesives, membranes, and even specialized materials not yet available on the public market.
- Engineering Services, including material identification & selection, process engineering, and analysis/testing (e.g. consultation on CAD designs, lab evaluation of materials).
Below, we provide more details on two prototypical solutions with a broad range of applications, plasma surface modification and specialized membranes for filtration. These solutions demonstrate not only EMD’s technical expertise, but our commitment to working hand-in-hand with clients to understand their problem, analyze it in-depth, and pinpoint an appropriate solution.
In many cases, EMD clients don’t initially know what technology they need and that’s okay. Our approach isn’t centered on marketing a particular material, process, or technology, but instead on true solutions engineering. Careful material selection, supported by advanced enhancements, can solve a huge variety of problems—in many cases problems clients didn’t even know they had.
What is Plasma Surface Modification and why does it matter?
Plasma treatment is a great example of a materials engineering technique that can directly enhance key material properties. Used in a wide range of industries, this surface modification process can prime nearly any surface for improved acceptance of secondary manufacturing applications.
We explore the basics of plasma surface modification below. For a more in depth look at this technology and its applications, we recommend our whitepaper here.
How does plasma surface treatment work?
This reactive treatment is used to modify the traits of a material’s surface on a molecular level.
TriStar’s EMD division uses a low-pressure “vacuum plasma” methodology, which helps achieve the most consistent, longest lasting surface treatments possible. A material is placed into a vacuum chamber which is emptied of air and reduced to an extremely low pressure. A mix of gases is injected into the chamber and subsequently ionized via electrical charge, generating plasma ions. Ions react with the surface of the material in the chamber, with different results achieved through different plasma types, pressures, and length of treatment.
Ceramics, polymers, elastomers, and metal assemblies can all be treated via plasma surface modification. This treatment provides a great example of how an upstream material enhancement can drive valuable downstream benefits. Early-stage plasma treatment, for example, can actually boost yield by reducing defects caused by insufficiently bonded paints, inks, molding, and other coatings. And, compared to traditional solvent chemistry solutions like acetones or sodium naphthalene, plasma is less caustic and much more environmentally friendly.
You can learn more about “Plasma 101” in a talk with EMD engineer Frank Hild here.
Common Applications for Surface Modification Plasma Treatment
- Altering material surfaces at a microscopic level to improve bonding properties.
- Micro-cleaning a surface, which can enhance wetting of adhesives or over-molded elastomers.
- Functionalizing groups (carbonyl, hydroxyl, and others) to improve surface energy.
- Enhance a material with hydrophobic or hydrophilic properties.
- Boost production yields through plasma treatment before secondary processes.
Plasma Surface Modification in Action
Plasma surface modification is a great fit for a wide variety of materials engineering challenges. The applications below provide some useful examples (with links to more detailed case studies for more information).
- You may even be able to find plasma-treated surfaces in your own mouth! Modern dental implants are made from titanium and other materials which fuse directly with the jawbone, imitating a natural tooth’s root. TriStar worked with a specialty implant clinic to develop a cold plasma treatment that allows for super-clean implants with maximum bond-ability. Learn more here.
- P-38 Lightning fighter aircraft have been shooting through the sky with their unique, twin-boom fuselage since World War Two. Military collectors keep these tributes to history in the sky today—with the help of TriStar plasma surface modification. In this case, a releasing agent helped release urethane control yokes from their mold, but prevented successful paint application. Plasma treatments bridged this gap, restoring paint adherence even after the releasing agent had been applied. Learn more here.
- Catheters (flexible, hollow tubes used to create a channel for the passage of fluids or a medical device into the body) are a critical medical device that must be super-clean. They must also be incredibly slick to slide through bodily veins without causing damage. TriStar worked with medical device OEMs to develop a plasma treatment that helps a powerful lubricant adhere tightly to catheters. You’ll also find plasma being used on other medical devices such as drainage tubes, endoscopes, and intraocular lenses. Learn more here.
Specialized Polymer Filtration Membranes
Membranes are simply thin sheets of semi-permeable material. Properly engineered, they can be used in a variety of filtration applications, including removing water contaminants like bacteria, particulate matter, and parasitic microorganisms.
By using different materials and engineering them to have different microporous structures, different filtration outcomes can be achieved. By allowing some substances through but not others, membranes can be used to purify a liquid of toxins, separate substances for further analysis, or in food preparation.
TriStar EMD takes pride in the customizability, consistency, and reliable delivery of specialized membrane solutions. Many specialty product areas (like medical devices and automotive) which utilize filtering membranes also feature a high rate of innovation and relatively short product life spans (often ~5 years). Consequently, large inventories risk going to waste; TriStar offers the timely supply needed to maintain lean inventories and order more membranes on an as-needed basis.
What kind of materials are used for filtration membranes?
PTFE membranes are one of the most commonly specified for water filtration in the food industry. PES (polyether sulfone) is another common choice, as it can be readily manufactured with precise, reproducible properties (with pore sizes that can be specified all the way down to 40 nanometers). Other common material choices include PVDF (Polyvinylidene Fluoride), Nylon, and PP (polypropylene).
Common Applications for Membrane Filtration
- Whole Blood Separation
- Molecular Assay Reagent Mixing
- Fuel System Phase Separation
- Hydroponics
Asymmetric v. Symmetric Membranes
Membranes are commonly classified as either symmetric or asymmetric. Asymmetric membranes exhibit varying pore size, while symmetric are more uniform. By combining different membrane layers with different pore sizes, asymmetric membranes can generally be used to achieve more targeted, high-performance filtering outcomes. TriStar EMD has the capability to fabricate both symmetric and asymmetric membranes.
Specialized Membranes in Action
Polymer membranes can be engineered for a wide variety of filtration use cases, ranging from medicine to food and beverage processing.
- A TriStar client was looking for a path to improve the performance and accuracy of their High-Performance Liquid Chromatography (HPLC) system. This analytical chemistry process is used to identify and quantify each part of a chemical mixture. An absorbent material is used to generate differential flow rates of a mixture as it flows through. TriStar created a novel membrane, Ultraflon M18+, specifically designed with hyper-hydrophilic properties which allow for more precise control over liquid and gas flow. Learn more here.
- On-device, “In Vitro Diagnostics” (IVD) is used to analyze samples taken from the human body. IVD medical devices rely on membranes to separate blood plasma. Blood plasma testing is commonly used, for example, to highlight antibody markers and for molecular testing. TriStar worked with blood testing device OEMs to develop Ultraflon M10 PES, a specialized asymmetric membrane which can achieve fast plasma separation while minimizing assay interference. Learn more here.
Value Added Consultative Engineering Services
Advanced polymer solutions like plasma surface treatments and precision engineered filtration membranes can offer incredible value in the right applications. EMD’s technological capabilities to deliver these services, however, is only a small part of the overall value we provide clients. Our EMD services give clients access to an advanced materials engineering team that’s perfect for a variety of scenarios:
- In house engineering teams are overworked and desperately need help selecting the right material for a critical application.
- Engineers on staff are skilled in their own specialty area but lack specialized materials enhancement knowledge (or up to date knowledge in this incredibly fast-moving field).
- A chronic problem is proving a tough nut to crack, and in-house engineers need a fresh set of eyes with extensive experience tackling complex, nuanced materials engineering problems.
In any of these scenarios, clients can leverage EMD for end-to-end solution engineering. That means studying the application in depth (including operating environment, functional requirements, maintenance needs and availability, budget, and component lifespan), identifying the right solution, testing it as necessary, and supporting successful implementation in the field.
Not every problem requires an advanced, “enhanced materials” solution, and EMD is backed by TriStar’s extensive portfolio of materials that can solve many engineering problems off the shelf. Crucially, EMD clients don’t need to know anything about plasma, specialized membranes, or other advanced manufacturing technologies to get the process started. Instead, they can simply reach out to EMD and describe their problem.
TriStar Engineering Services Offer:
- Deep knowledge of advanced material enhancement processes like plasma treatment and membrane fabrication. These processes are essential to getting your materials to perform in challenging applications or production processes, but many manufacturers cannot afford to maintain in-house expertise on these fast-developing technologies.
- Extensive ground-level experience across a broad range of industries. TriStar’s EMD engineers aren’t just laboratory experts. They are applied engineers with in-depth experience specifying and delivering solutions that are carefully geared to cost targets, performance requirements, and long-term maintenance considerations.
- A dedication to high-touch service that goes beyond selling materials. Larger polymer suppliers are often focused on securing massive bulk orders. In our experience, lower volume applications requiring unique engineering often fall through the cracks at the largest suppliers.
The EMD team is focused on working directly with customers of all sizes. Our margins don’t depend on bulk orders, and no use case is too small to bring EMD’s expertise to bear. Our blog here takes a more in-depth look at TriStar’s engineering partnership with clients of all sizes.
Frequently Asked Questions
Here are a few common questions relating to the content in this guide.
Q: What is TriStar’s Enhanced Materials Division (EMD)?
A: The Enhanced Materials Division (EMD) is a full-service solution team, providing surface enhancements, product offerings, and engineering services for challenging materials engineering problems.
Q: How does EMD work with clients?
A: EMD works effectively as an auxiliary engineering team for TriStar clients, partnering to tackle complex challenges.
Q: What types of services does EMD offer?
A: EMD offers surface enhancements, advanced product offerings (like adhesives and membranes), and engineering services such as material selection and process testing.
Q: What is plasma treatment and how does EMD use it?
A: Plasma treatment is a surface modification technique, and EMD uses low-pressure “vacuum plasma” to modify ceramics, polymers, elastomers, and metal assemblies.
Q: Why use plasma treatment for materials?
A: Plasma treatment is an upstream enhancement that drives downstream benefits—like improved bonding—by modifying surfaces at the molecular level.
Q: What are specialized membranes in EMD’s offerings?
A: Specialized membranes are semi-permeable thin sheets, engineered with microporous structures to achieve tailored filtration results.
Q: How does EMD ensure quality with membranes?
A: EMD ensures quality by providing customizable, consistent, and reliable delivery of specialized membrane solutions.
Q: What makes EMD’s value proposition beyond materials?
A: Technology is just the start—EMD adds value by giving clients access to an advanced materials engineering team for holistic, end-to-end solutions.
Q: How does EMD approach challenging materials problems?
A: EMD starts by studying the full application—environment, requirements, and maintenance—then engineers a materials-driven solution tailored to the challenge.
Q: What engineering approach does EMD use in consultative projects?
A: EMD applies a systems-thinking approach—studying the full application, operating conditions, and materials environment to engineer tailored, value-added solutions.